In the fast-paced manufacturing landscape, where precision and efficiency are paramount, the manual counting process must be monitored to ensure product quality and packaging accuracy. This article explores a transformative solution – Iwoweight – designed to elevate and enhance manual counting practices. Delve into the following pages to discover how integrating Iwoweight can streamline your quality checks and significantly improve accuracy in packaging processes, offering a comprehensive approach to optimising manual counting in the manufacturing domain.
What Equipment is Essential for Product Packaging and Counting?
When counting products manually, selecting the proper hardware is crucial, as it determines how efficiently signals are transmitted—each representing a registered product cycle. Explore the various hardware options tailored for this task.
Sensor
Weight sensors are dependable options that generate signals for each product registered during the cycle. They are applicable in both manual counting and automated production lines. The accompanying image vividly illustrates the effectiveness of product counting through sensor usage, a widely acknowledged method prevalent in the industry.
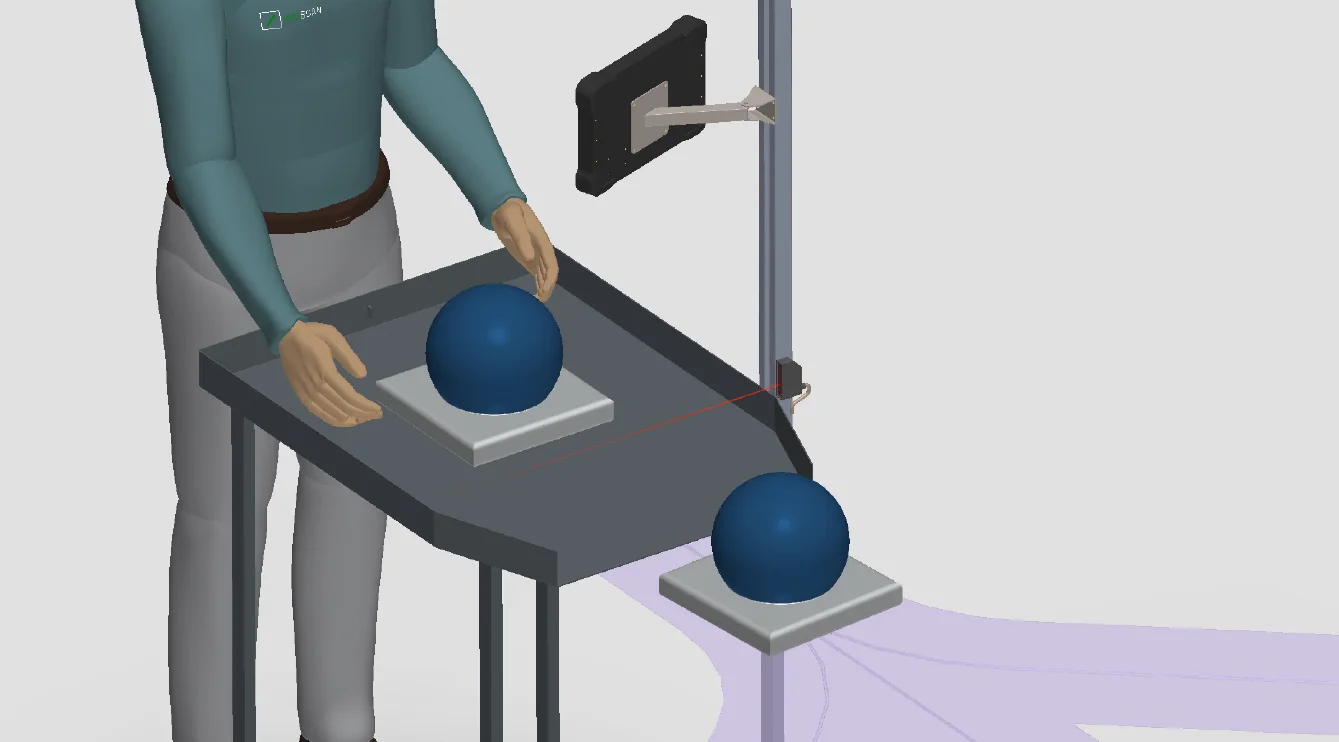
Iwoweight device
This miniature computer is an effective hardware solution for seamless signal transmission. Incorporating a small computer directly connected to your equipment (manual or automated), Iwoweight stands out as a sophisticated option, particularly prevalent in newer computerised machines. Iwoweight solution enables the swift detection and resolution of many issues, and Iwoweight outputs also boast increased stability compared to sensor outputs. Furthermore, the Iwoweight device serves a dual purpose for product counting, accurately measuring machine cycles and determining operator work time. The image above showcases Iwoweight seamlessly utilising a PLC in an electric cabinet.
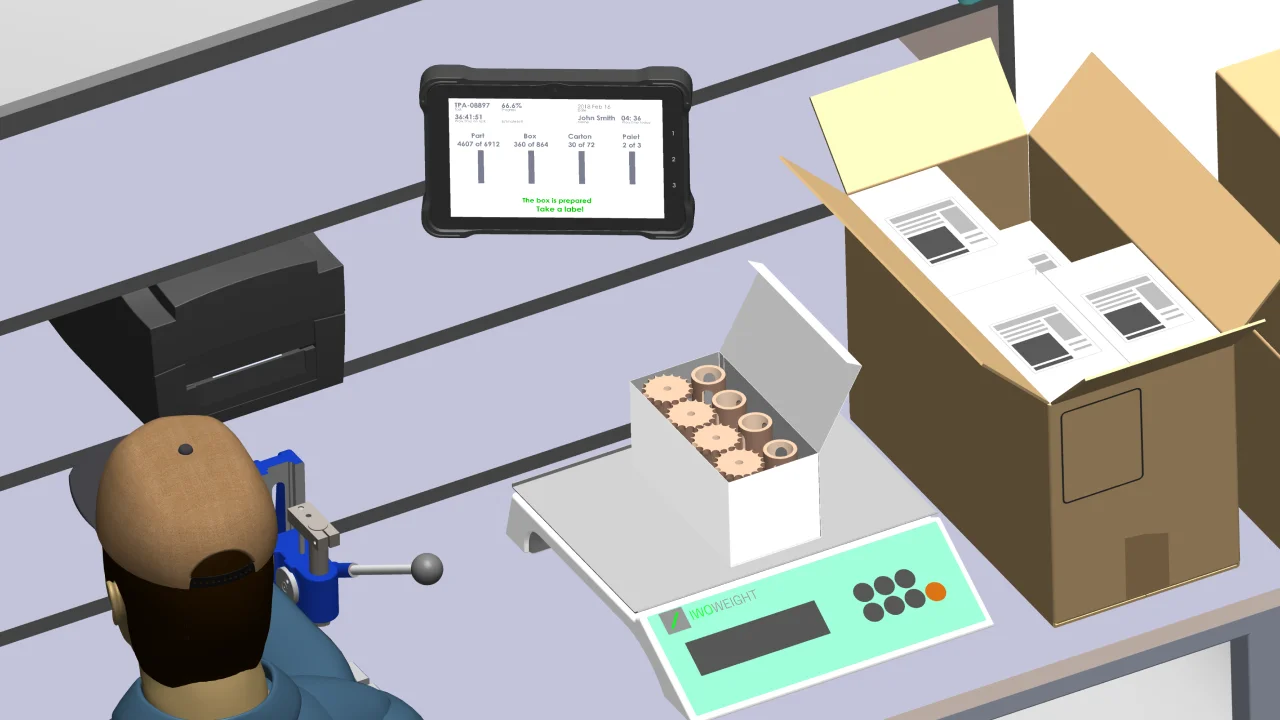
Button (the manual touch)
A hands-on approach where a signal is triggered manually by pushing a button. When automated solutions are unfeasible, the manual counting approach becomes viable by installing a push-button, mainly in productions where product quality is variable. By pressing a few buttons, the operator can ascertain the quality factor of a product. For example, the same type of meat can exist in various variations.
Operators manually press this button upon completing a product. While not the most foolproof method, it proves practical in scenarios involving intricate, time-consuming, large, or custom products. For a detailed exploration of button usage and its relevance in diverse production scenarios, refer to our article on other types of production.
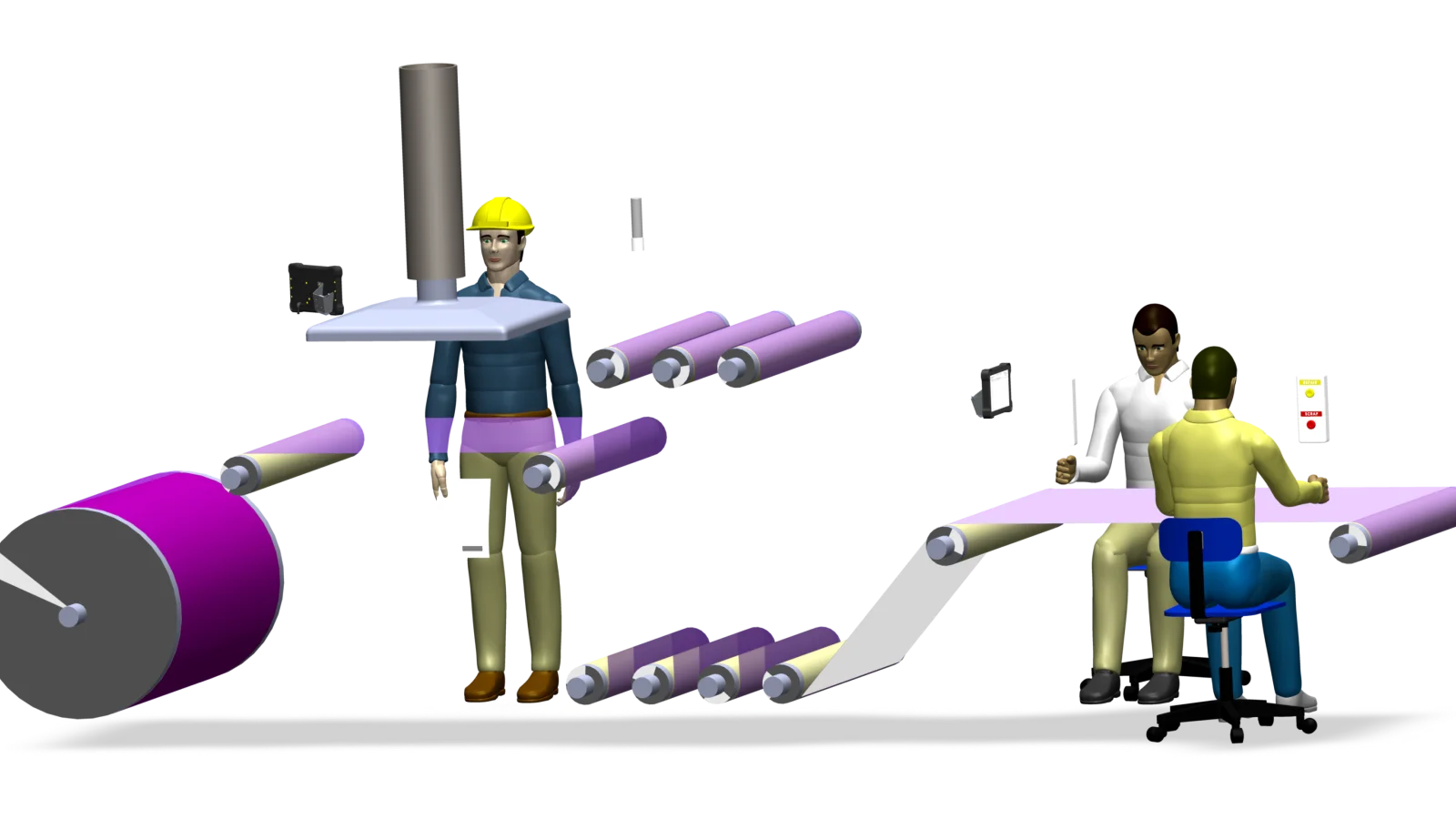
Any Electrical System with a Relay
Count products by connecting them to an array of electrical systems through a relay. This method finds application in CNC machines, exemplifying a specialised case. Programming a modern CNC machine allows it to close a relay on a circuit board upon completing a part. If you possess a CNC machine, delve into our article on monitoring CNC machines for comprehensive insights.
All collected data accessible via HTTP(S) or web socket requests
Access data from any workstation seamlessly through HTTP(S), web sockets, or a web browser. Explore a revolutionary method that eliminates the need for physical hardware, relying instead on secure HTTPS requests. Additionally, it conveniently views all workstations in a single window, organised based on specified criteria.
Holistic Integration for Streamlined Operations
While individual solutions may address specific needs, the true power lies in an integrated system that seamlessly incorporates all options and adapts to the unique demands of your manufacturing environment. Enter Iwoweight, an all-encompassing solution to revolutionise data capture, processing, and utilisation in your manufacturing operations.
Iwoweight goes beyond fragmented solutions by offering a comprehensive, all-in-one package. This integrated approach ensures that every facet of your production process is covered, eliminating the need for piecemeal solutions that may not communicate effectively with each other. Iwoweight's seamless interconnection is tailored to meet the specific demands of your manufacturing workflow, providing a unified and efficient solution.
Efficient Hardware Signal Capture
The Iwoweight system's heart is its sophisticated hardware, designed to capture all signals emanating from your production environment. This includes signals from sensors, PLCs, buttons, relays, or any other electrical system, creating a unified data stream that forms the foundation of accurate and comprehensive manufacturing insights.
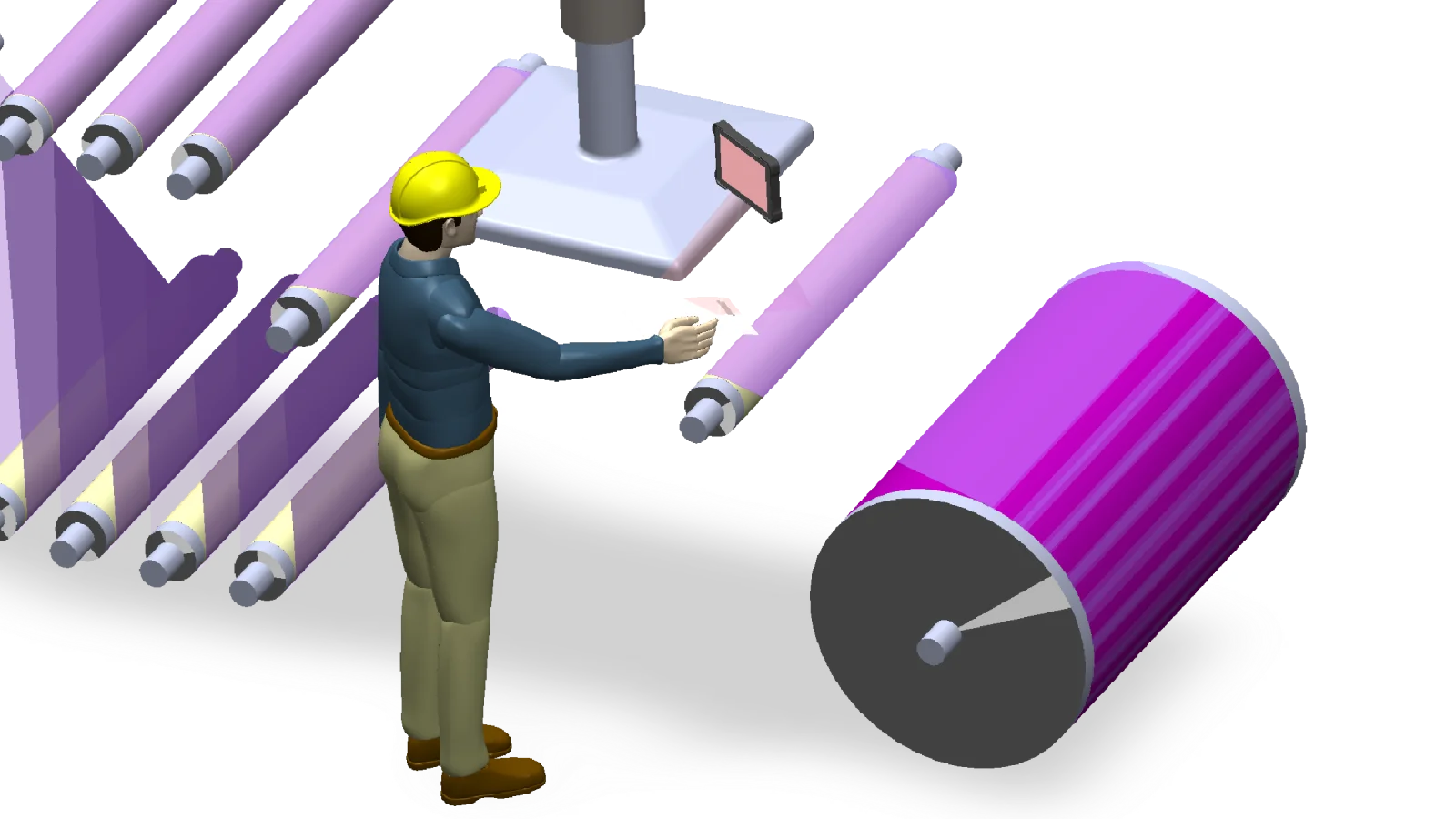
Swift Data Transmission to Servers
Once signals are captured, Iwoweight's hardware transmits this valuable data to dedicated servers. This swift transmission ensures no delay in processing critical information, allowing for real-time analysis and decision-making.
Instantaneous Data Processing
The true magic of Iwoweight unfolds as the system swiftly processes the transmitted data and, acting as a digital maestro, orchestrates the harmonious integration of signals, translating raw data into meaningful insights. This instantaneous processing capability ensures immediate access to accurate and up-to-the-minute data, providing a real-time pulse on your manufacturing operations.
Unlocking Full Potential for Manufacturing Excellence
Iwoweight's real-time feedback loop is not just about speed; it's about unlocking the full potential of your manufacturing operations. Providing immediate access to accurate data, Iwoweight empowers you to make informed decisions, optimise processes, and enhance efficiency. The seamless integration, efficient signal capture, and swift processing form the trifecta that propels your manufacturing operations to new heights.
Embrace the future of manufacturing with Iwoweight, an integrated solution that meets expectations and redefines them, ushering in a new era of simplicity, accuracy, and operational excellence.
Empower Your Manufacturing Setup
At Iwoweight, we furnish you with the essential hardware components to integrate our solutions seamlessly into your manufacturing environment. The Iwoweight’s IIoT device, accompanied by a reliable power supply, is central to this offering.
The image below provides a visual guide to the Iwoweight setup, illustrating the connections to the network and display devices. For a more in-depth understanding of the Iwoweight setup process, we invite you to explore our dedicated article on configuring Iwoweight, where we walk you through the steps to optimise your manufacturing environment. Elevate your operations with Iwoweight, where hardware meets efficiency, and simplicity transforms your manufacturing landscape.
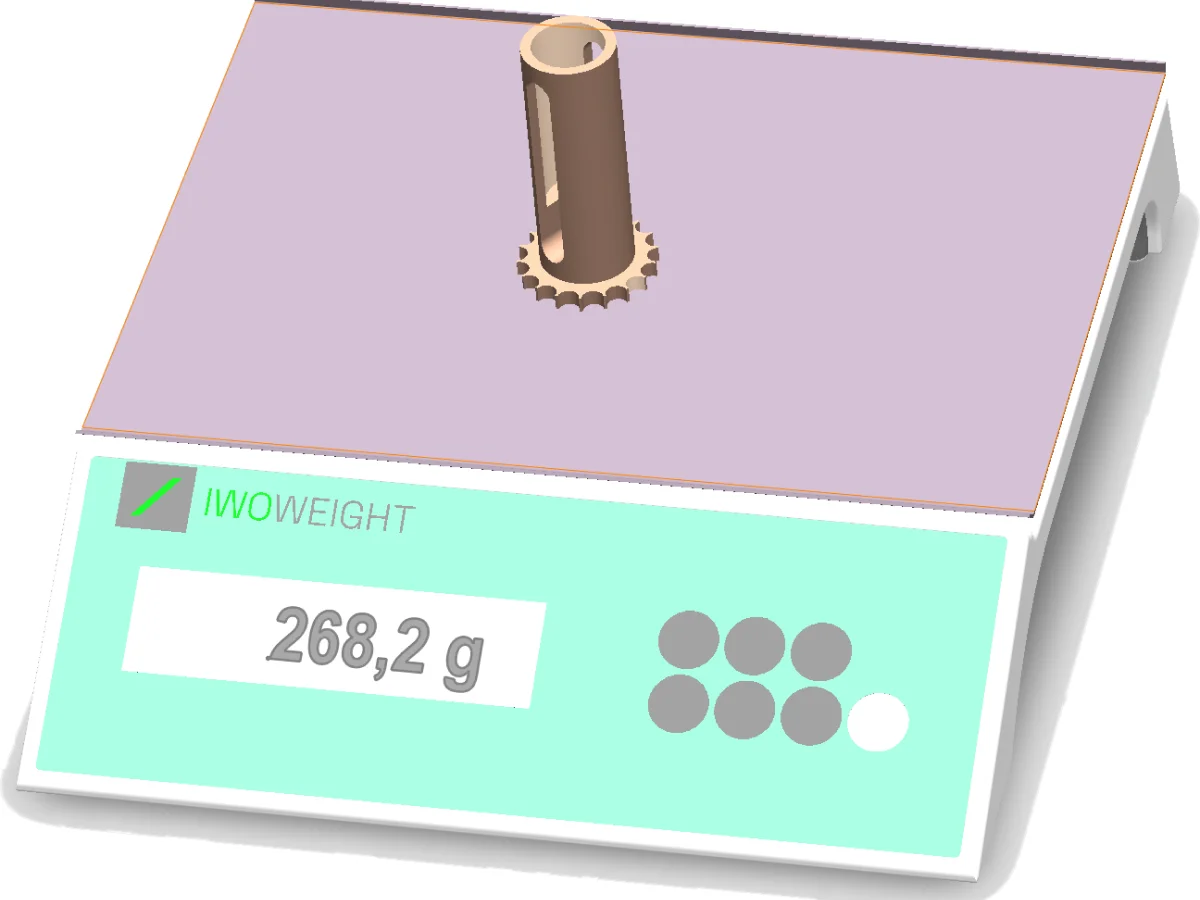
Iwoweight's Unit Conversion Capabilities
In the dynamic manufacturing landscape, the need often arises to translate product counts into diverse units, whether kilograms, meters, or other designated measuring units, transcending the conventional realm of mere numerical representation. Iwoweight steps in as a game-changer, offering a range of benefits tailored to the intricacies of the manufacturing industry.
Unit Conversion for Enhanced Insight
Our system provides invaluable insights by seamlessly converting signals into alternative forms of information. Picture this: you're in the business of packing bags, and your focus is on monitoring production in terms of weight. Iwoweight effortlessly caters to this need by allowing you to configure the system and convert each product into your chosen weight unit.
Flexible Conversion Definitions
Adaptability is at the core of Iwoweight's functionality. The system accommodates many conversion definitions, ensuring a tailored approach to meet your requirements. A different conversion definition seamlessly takes the reins as you transition from one product to another. This flexibility empowers you to customise your monitoring based on the unique characteristics of each product within your manufacturing lineup.
Diverse Conversion Possibilities
Beyond weight conversion, Iwoweight facilitates the transformation of product counts into various other numerical representations. For instance, if your sensors primarily register boxes of products, but you desire an overview of the total number of individual products within the system, Iwoweight effortlessly enables this transition. The system's adaptability ensures you can choose the unit that aligns perfectly with your monitoring goals.
Embrace the versatility of Iwoweight, where unit conversion becomes a seamless and integral part of your manufacturing process. Elevate your insights, enhance your decision-making, and usher in a new era of precision and adaptability with Iwoweight's transformative capabilities.
What is Iwoweight?
In pursuing precision in manufacturing data, Iwoweight introduces a groundbreaking feature that significantly elevates the reliability of your production insights. The concept is simple yet powerful—utilise a control signal to validate the authenticity of primary signals, providing a fail-safe mechanism to ensure the accuracy of your OEE data. In simple words, Iwoweight is a game-changing hardware tool for manual packaging and quality control processes, from meticulous weight monitoring to customised stickers and real-time work hour tracking. It seamlessly connects to scales and monitors package weights to ensure precision and identify deviations. Also, it can print customised stickers and track real-time work hours; Iwoweight is your solution for error-free packaging, cost efficiency, and precise task management, providing invaluable insights into your business processes.
Practical Validation in Action
Consider scenarios where verifying signals becomes imperative to prevent inadvertent disruptions to your OEE data. For instance, during maintenance or cleaning processes, you want to shield your data from accidental signals triggered by sensors. Iwoweight seamlessly addresses this challenge by incorporating a secondary signal and adding an extra validation layer to your production data.
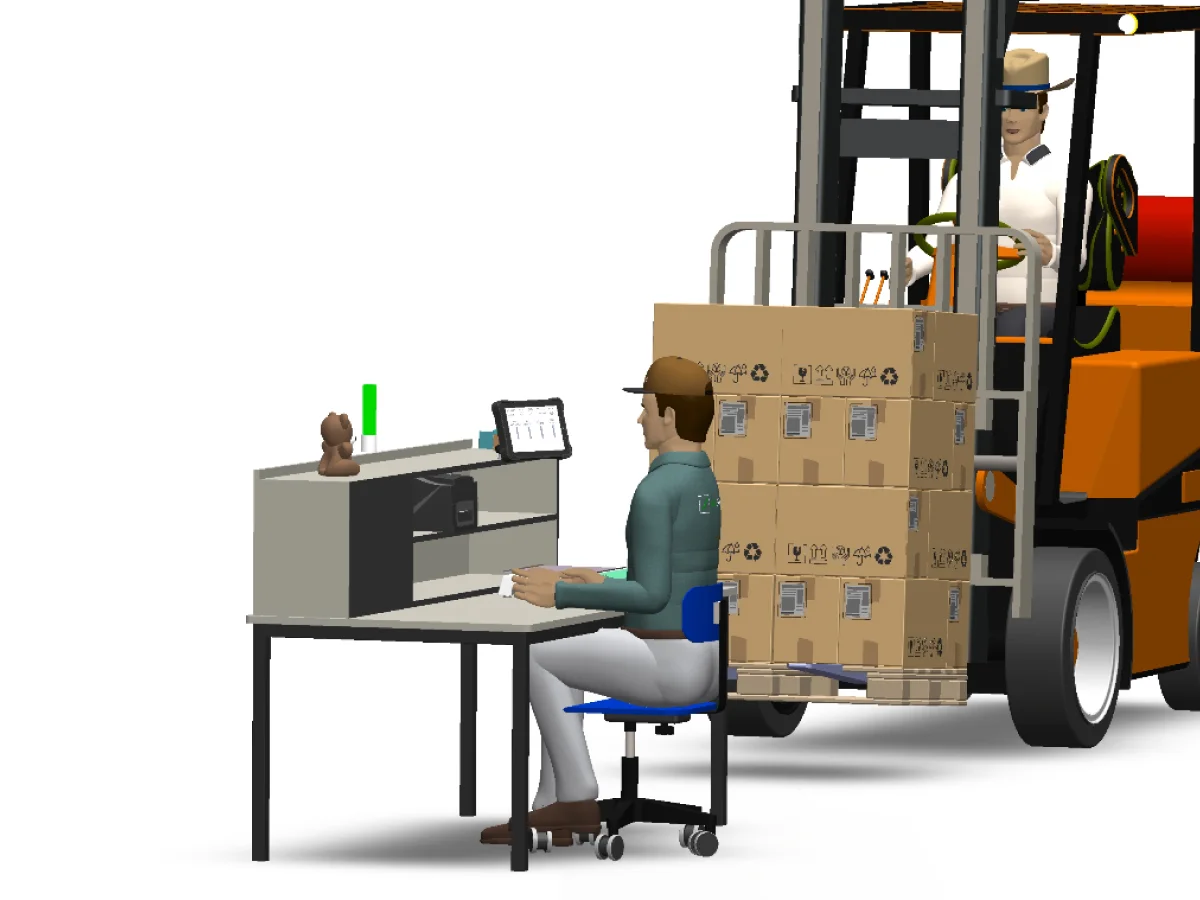
Precision in Extrusion Processes
In intricate manufacturing processes like pipe extrusion, where precision is paramount, Iwoweight steps up to the plate. By leveraging multiple control signals from the machine, you gain unparalleled accuracy in your production data. This strategic use of control signals ensures that each data point is meticulously validated, providing a comprehensive and dependable overview of your manufacturing efficiency.
Dual Signal Dynamics
The implementation is straightforward yet effective—product signals are tallied only when the control signal is ON, guaranteeing that your data remains unaffected by extraneous factors. Conversely, when the control signal is OFF, the system intelligently disregards any signals from the sensor, preventing data distortion during maintenance or cleaning activities.
Seamless Integration with Andon Lights
Take a closer look at the synergy between primary and secondary signals. In the presented example, the direct signal originates from the sensor, while the secondary signal is sourced from the Andon light. When the Andon light illuminates, Iwoweight's device registers sensor signals as usual. However, when the Andon light is extinguished, it acts as a sentinel, ensuring that all sensor signals are discreetly ignored, preserving the integrity of your manufacturing data.
Empower your manufacturing insights with Iwoweight's dual signal control, where precision meets practicality and data reliability takes centre stage. Elevate your OEE metrics and extrusion process monitoring with a solution that provides dependable and accurate manufacturing intelligence.
What do you get by buying Iwoweight?
Are you tired of packaging errors and quality control mishaps? Say hello to Iwoweight, the hardware standalone wizard about revolutionising your manual packaging processes!
Embarking on the Iwoweight journey means embracing unparalleled advantages tailored to elevate your manufacturing operations. Let's delve into the myriad benefits you unlock when you choose Iwoweight for your production needs.
Precision Packaging
Connected to scales, Iwoweight diligently monitors and registers the weight of each package. No more wondering if there's misconduct or if the package matches the specific weight. It's your vigilant quality control partner.
Error Eradicator
Bid farewell to packaging errors. Once the packaging is done, Iwoweight will print a customised sticker (logo, weight, date, operator name, and more) for you. It's cost-efficient and saves valuable workforce.
Real-Time Work Hours
But wait, there's more! Iwoweight doesn't stop at packaging. It's your go-to tool for monitoring your team's real-time working hours. Forget clunky check-in and check-out systems; it's all about precision task management and exact working hours.
Business Insight Guru
Ready for a game-changer? Iwoweight isn't just a monitoring tool; it's your key to unparalleled business insights. Gain a holistic view of your operations, identify areas for improvement, and elevate efficiency to new heights. With Iwoweight, your bottom line receives a well-deserved boost, ensuring sustainable success in the manufacturing realm.
What are the application avenues for Iwoweight?
Iwoweight's versatility knows no bounds, making it an indispensable tool across various industries. No matter your industry, Iwoweight is the secret to precision, cost savings, and quality assurance in your packaging and quality control processes.
Manufacturing Excellence
Streamline your manufacturing operations by ensuring precise packaging and quality control. Iwoweight's real-time monitoring prevents errors and enhances product consistency.
Logistics and Distribution
In the world of logistics, accuracy is vital. Iwoweight guarantees that packages meet weight requirements before they hit the road, reducing costly shipping errors.
Food and Beverage
Maintain impeccable quality standards in the food and beverage industry with Iwoweight. From portion control to quality checks, it's your trusty companion.
Retail and E-commerce
Elevate the customer experience by ensuring accurate and consistent packaging. Iwoweight helps you meet shipping regulations, minimise returns, and save on labour costs.
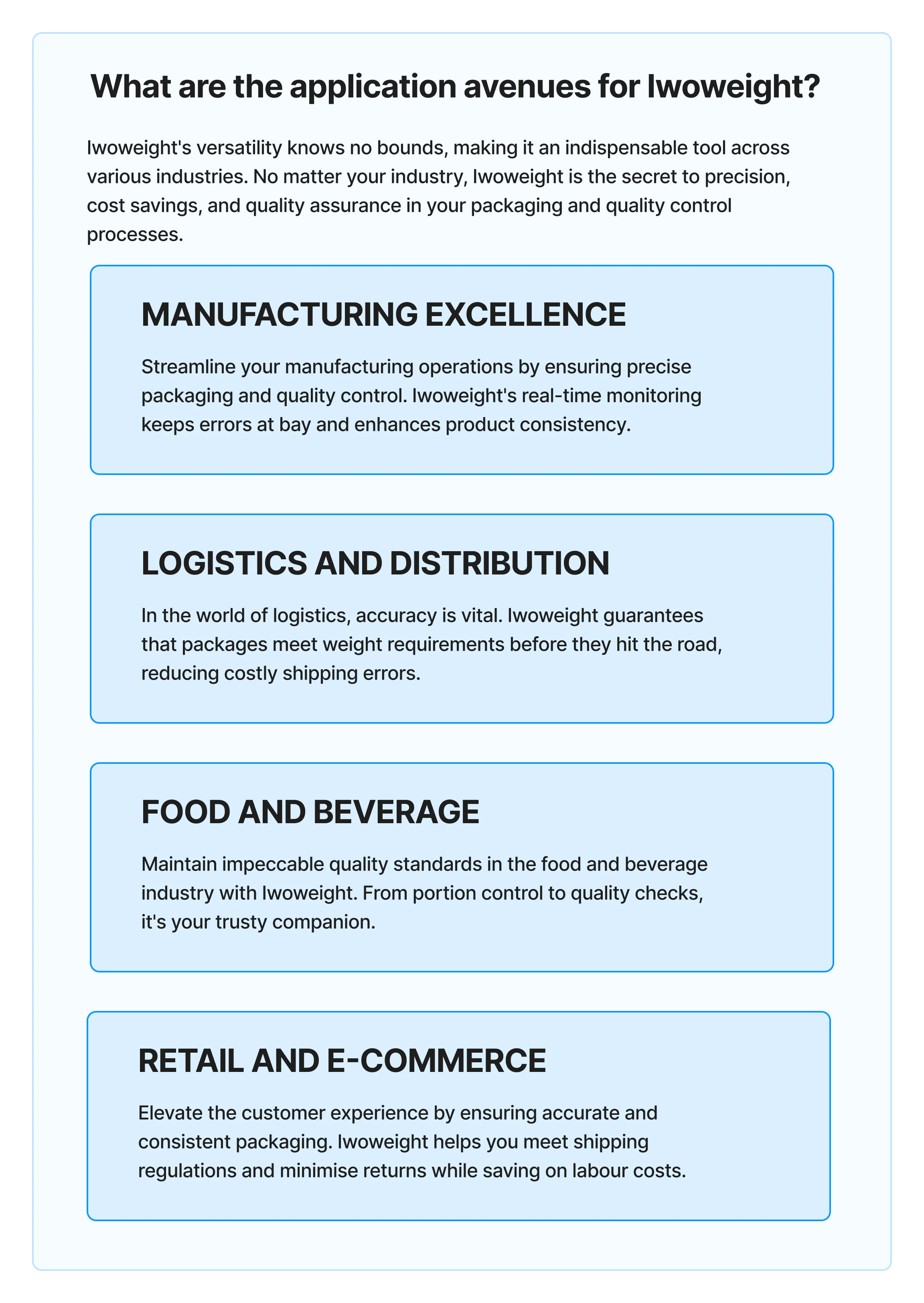
Comments
No comments yet!Add a Comment
You must be logged in to post a comment.