Manufacturing environments are dynamic, often operating with precision and efficiency to meet demanding production schedules. In the heart of this intricate dance of machinery lies a crucial practice—preventive Maintenance (PM). As a proactive approach to equipment upkeep, preventive maintenance is a strategic endeavour that holds the key to enhancing equipment reliability, minimising downtime, and extending the overall lifespan of manufacturing assets.
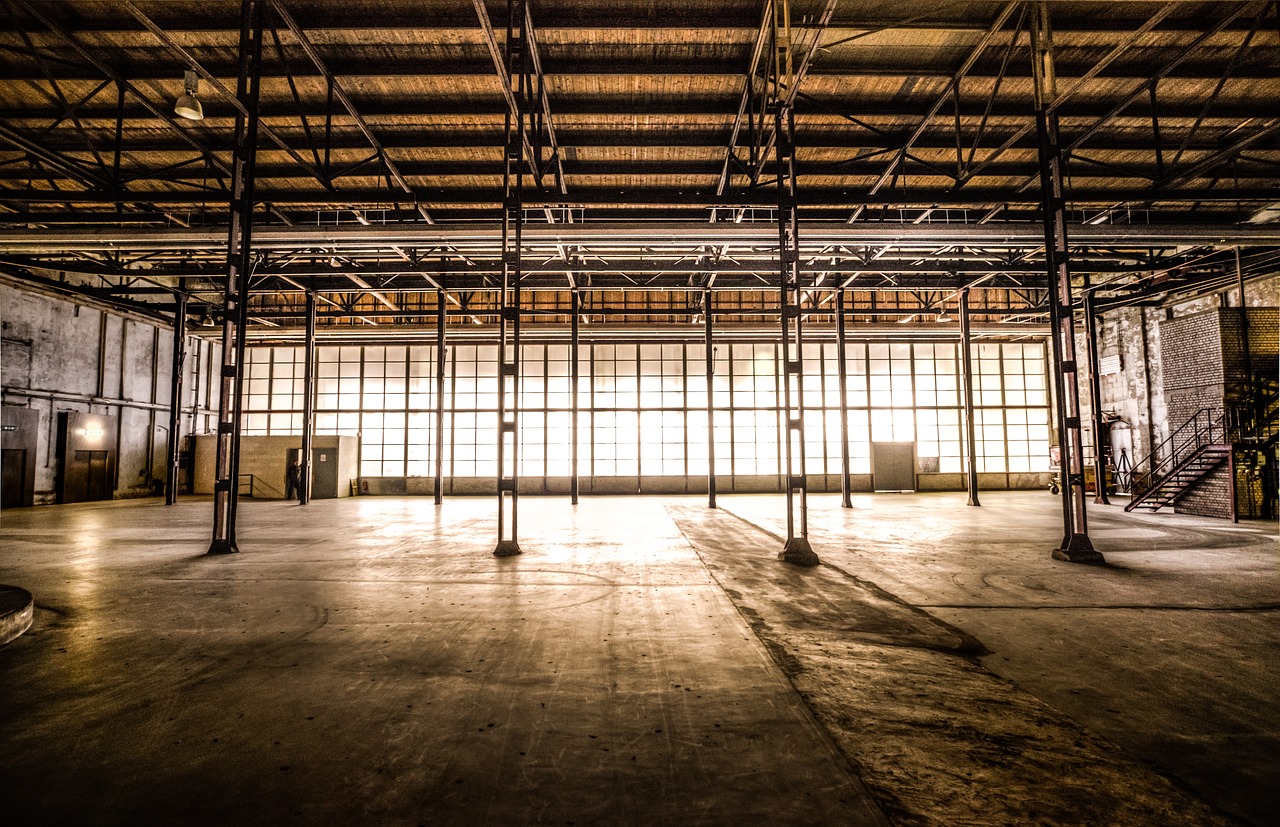
Significance of Preventive Maintenance
Overview of Preventive Maintenance
At its core, preventive maintenance is a systematic and planned approach to maintaining equipment and machinery. Unlike reactive maintenance, which addresses issues after they occur, preventative maintenance is a proactive strategy aimed at identifying and addressing potential problems before they impact operations. It involves a combination of scheduled inspections, lubrication, adjustments, repairs, and component replacements to ensure that equipment operates at peak efficiency.
Importance in Manufacturing
In the fast-paced world of manufacturing, where every minute of downtime can have significant financial implications, preventive maintenance is a linchpin. Its importance lies not only in averting costly breakdowns but also in optimising production efficiency. By addressing potential issues before they escalate, manufacturing plants can minimise disruptions, maintain consistent product quality, and uphold the trust of customers and stakeholders.
Impact on Equipment Efficiency and Longevity
The impact of preventive maintenance extends beyond immediate operational concerns. Efficiently maintained equipment operates at its full potential, delivering higher output with fewer interruptions. This, in turn, directly contributes to the longevity of machinery. Preventive maintenance helps preserve the integrity of critical components, reducing the likelihood of unexpected failures and ensuring that equipment continues to perform at its best throughout its lifecycle.
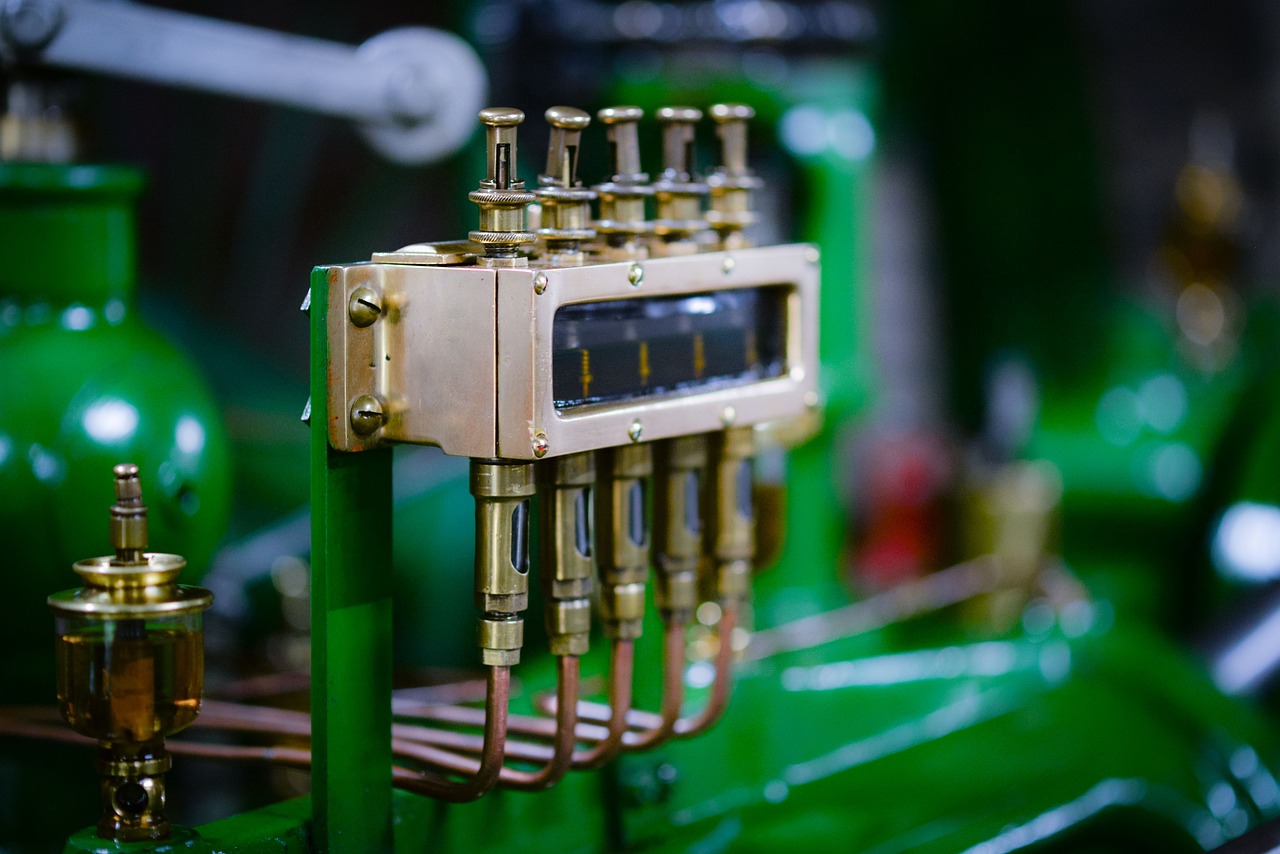
Routine Inspections
Definition and Purpose
Regular Equipment Checkups
Routine inspections involve scheduled, regular checkups of equipment and machinery to assess their condition. This proactive approach allows maintenance teams to identify any signs of wear, potential issues, or deviations from optimal performance before they escalate into larger problems. The goal is to catch and address issues early, minimising the risk of unexpected breakdowns.
Identifying Wear and Tear
The primary purpose of routine inspections is to identify wear and tear on equipment components. By closely examining critical parts, maintenance teams can detect early signs of deterioration, corrosion, or misalignment. Addressing these issues promptly helps prevent more extensive damage and ensures the longevity and reliability of the equipment.
Examples of Equipment Subject to Routine Inspections
Various types of equipment benefit from routine inspections. This includes but is not limited to.
Bearings and seals in machinery |
Conveyor systems and belts |
Pumps and motors |
Hydraulic systems |
Electrical wiring and connections |
Best Practices in Routine Inspections
Inspection Checklists
Establishing comprehensive inspection checklists is a fundamental practice in routine inspections. These checklists outline specific components and parameters that need attention during inspections. By following a structured checklist, maintenance teams can ensure that no critical aspects are overlooked. Checklists can be tailored to the unique requirements of different types of equipment.
Utilising Technology for Data Recording
Embracing technology enhances the effectiveness of routine inspections. Mobile devices, sensors, and digital tools can streamline the inspection process. Maintenance teams can record data in real time, including images or videos of identified issues. This not only facilitates more accurate documentation but also enables quick sharing of information with relevant stakeholders, expediting decision-making.
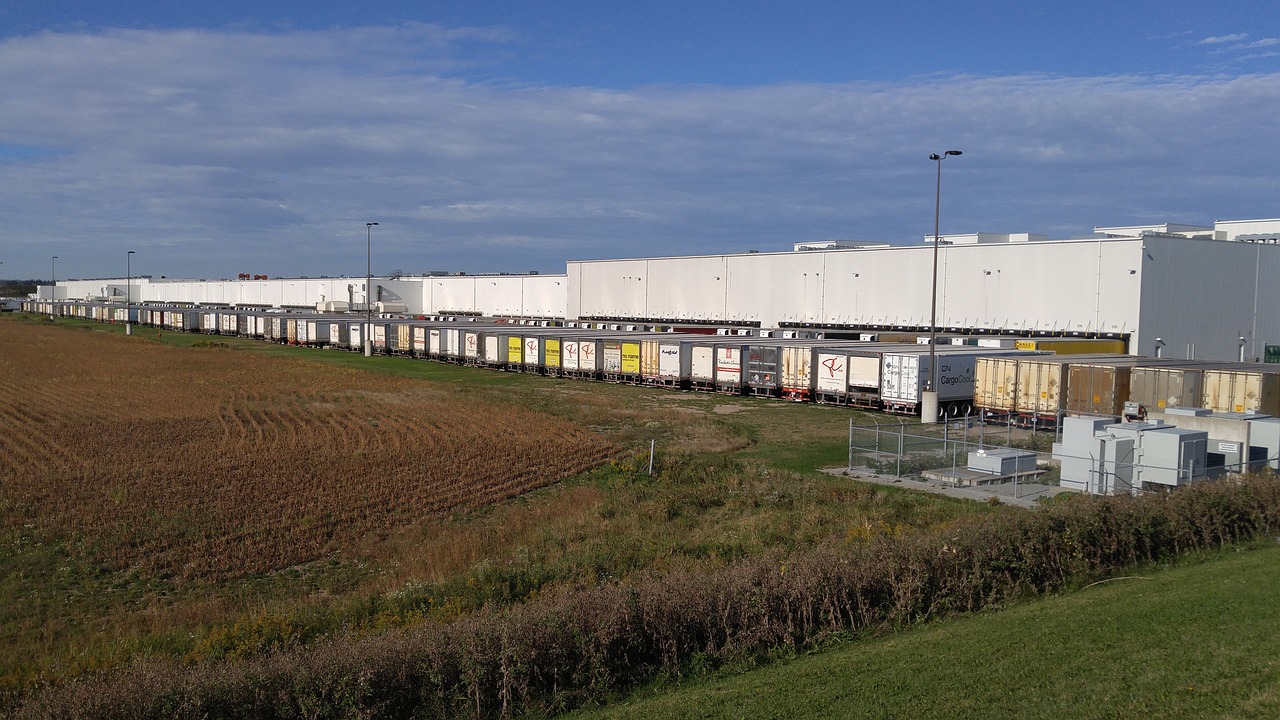
Integrating Findings into Preventive Maintenance Plans
The findings from routine inspections should be in collaboration with the broader preventive maintenance plan. Maintenance teams analyse inspection data to identify patterns, trends, or recurring issues. This analysis informs the adjustment of preventive maintenance schedules, component replacement plans, and overall equipment optimisation strategies.
Lubrication Schedules
The Role of Lubrication in Equipment Maintenance
Preventing Friction and Wear
Lubrication plays a crucial role in preventing friction and wear between moving parts of machinery. Friction is a natural consequence of mechanical operations, and without proper lubrication, it can lead to accelerated wear and damage. By introducing a lubricant between surfaces, the detrimental effects of friction are minimised, contributing to the overall longevity of the equipment.
Importance of Proper Lubrication
Proper lubrication is vital for the efficient functioning of machinery. It not only reduces wear but also dissipates heat generated during operation. Inadequate or improper lubrication can result in increased energy consumption, decreased efficiency, and, in extreme cases, catastrophic equipment failure. Establishing a consistent and effective lubrication schedule is, therefore, essential for equipment maintenance.
Common Lubrication Points in Manufacturing
Various components within manufacturing equipment require proper lubrication. Common lubrication points include.
Bearings and bushings |
Gears and gearboxes |
Chains and conveyors |
Hydraulic systems |
Sliding surfaces |
Establishing Effective Lubrication Schedules
Choosing the Right Lubricants
The selection of appropriate lubricants is a critical aspect of effective lubrication schedules. Different equipment and operating conditions may require specific types of lubricants, including oils, greases, or dry lubricants. Factors such as temperature, load, and speed influence the choice of lubricant. Maintenance teams must carefully assess these factors to ensure optimal performance and protection against wear.
Frequency of Lubrication
The frequency of lubrication depends on the type of equipment, operating conditions, and the selected lubricants. Over-lubrication can be as detrimental as under-lubrication, leading to excess lubricant buildup and potential contamination. Maintenance teams establish regular schedules for lubrication based on equipment specifications, manufacturer recommendations, and historical performance data.
Lubrication Equipment and Techniques
The methods and tools used for lubrication contribute to the effectiveness of the process. This may involve manual lubrication with handheld devices, automated lubrication systems, or centralised lubrication stations. The choice of equipment and techniques depends on the complexity of the machinery and the precision required for lubrication.
Component Replacement
Identifying Components Prone to Wear
Understanding Wear Patterns
Recognising wear patterns is essential for identifying components prone to deterioration. Maintenance teams analyse historical data and inspect components for signs of wear, such as abrasion, corrosion, or fatigue. Understanding these patterns allows for the prediction of when a component is likely to reach the end of its effective lifespan.
Predictive Analytics for Component Replacement
Leveraging predictive analytics enhances the accuracy of identifying components in need of replacement. By analysing data from sensors, monitoring systems, and historical performance records, maintenance teams can predict the remaining useful life of critical components. This proactive approach enables scheduled replacement before components fail, preventing unplanned downtime.
Examples of Critical Components
Certain components are particularly prone to wear and are critical for the overall performance of manufacturing equipment. Examples include.
Bearings in rotating machinery |
Seals and gaskets |
Belts and chains |
Cutting tools in machining equipment |
Electrical contacts and connectors |
Planned Replacement vs. Reactive Replacement
Benefits of Planned Component Replacement
offers several advantages. It allows maintenance teams to schedule replacements during planned downtime, minimising the impact on production schedules. This approach also reduces the likelihood of unexpected failures, optimising equipment reliability. Additionally, planned replacement can be more cost-effective than reactive replacement, as it avoids emergency repairs and associated downtime costs.
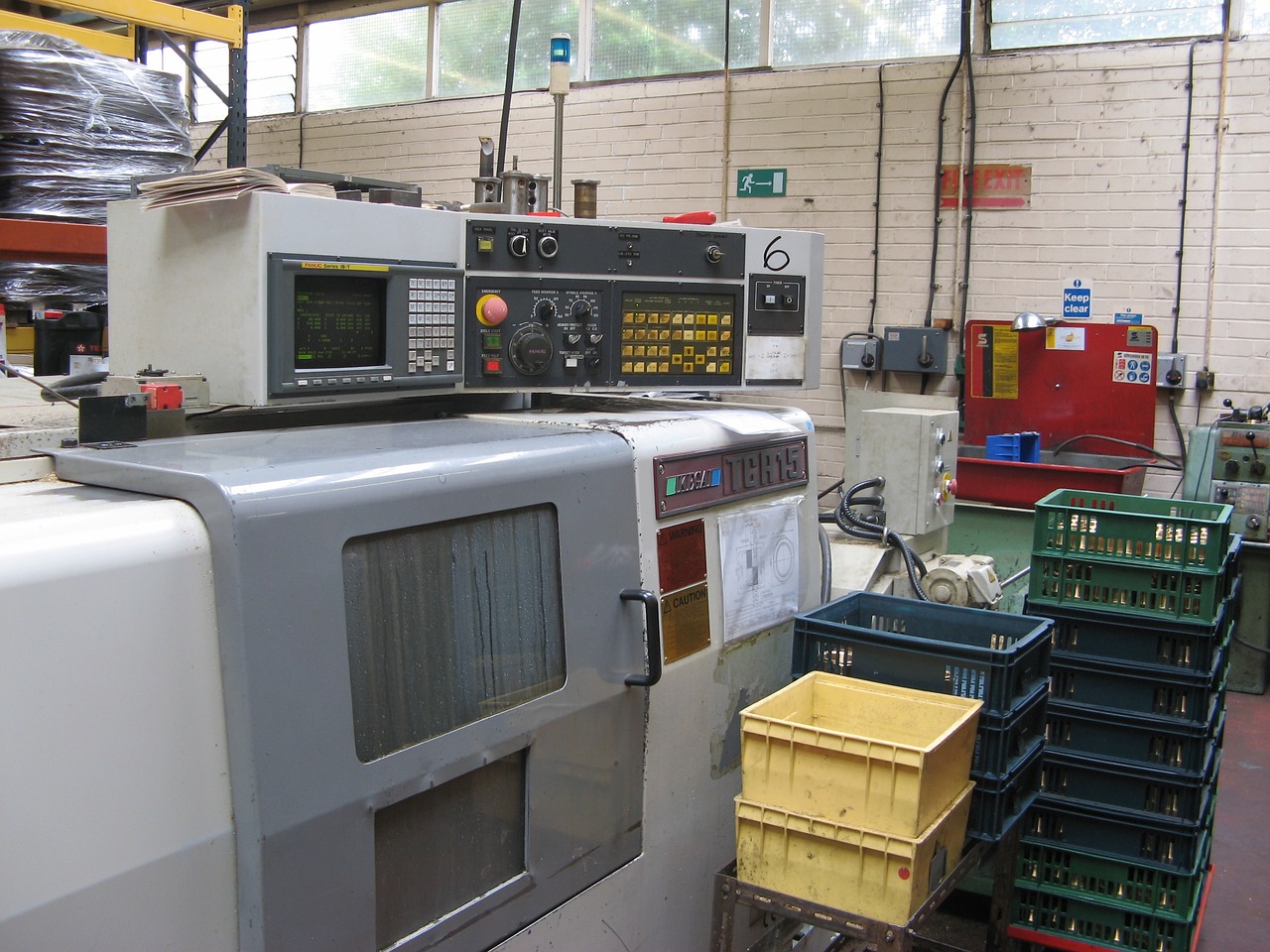
Risks and Costs of Reactive Replacement
Reactive replacement occurs in response to a component failure. This approach carries inherent risks, including extended downtime, production delays, and potential damage to other parts of the equipment. Reactive replacement may incur higher costs due to emergency repair services, expedited shipping of replacement parts, and the impact on overall productivity.
Strategies for Implementing Planned Replacement Programs
Implementing a successful replacement program requires careful planning and coordination. Strategies include.
Establishing a comprehensive asset inventory with replacement schedules |
Utilising predictive maintenance technologies for accurate scheduling |
Collaborating with equipment manufacturers for recommended replacement intervals |
Training maintenance personnel on the identification and replacement of critical components |
In the upcoming chapters, we will explore additional types of preventive maintenance, including calibration procedures and cleaning practices. Each practice contributes to the overall reliability and efficiency of manufacturing equipment, ensuring smooth operations and sustained productivity.
Calibration Procedures: The importance of calibration in manufacturing. Ensuring accuracy in measurements.
Calibration is fundamental to ensuring the accuracy and precision of measurements in manufacturing processes. Precision instruments and equipment require periodic calibration to maintain their reliability. Accurate measurements are crucial for quality control, compliance with standards, and overall process optimisation.
Types of Equipment Requiring Calibration
Various types of equipment in manufacturing demand regular calibration. This includes.
Measuring instruments (callipers, micrometres, gauges) |
Testing equipment (material testers, hardness testers) |
Analytical instruments (spectrometers, chromatographs) |
Process control instruments (temperature controllers, pressure gauges) |
Electronic equipment (oscilloscopes, multimeters) |
Regulatory Compliance and Calibration
Many industries are subject to regulatory standards that mandate regular calibration. Compliance with these standards is essential for quality assurance, meeting industry regulations, and ensuring the reliability of manufacturing processes. Calibration certificates and documentation are often required to demonstrate adherence to these standards.
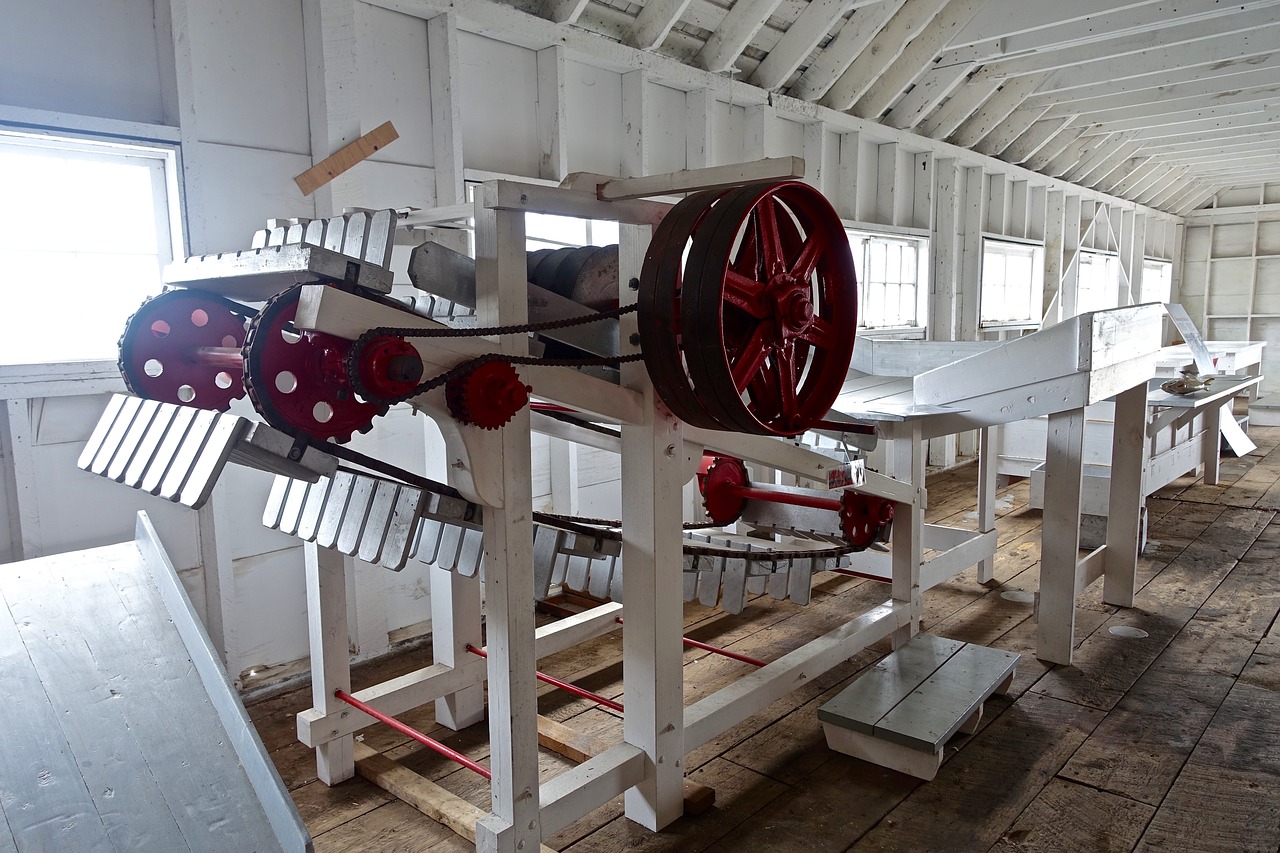
Implementing Calibration Procedures
Establishing Calibration Schedules
Calibration schedules outline when specific equipment or instruments should undergo calibration. These schedules are typically based on the manufacturer's recommendations, industry standards, and the frequency of equipment use. Well-established calibration schedules contribute to the consistency and accuracy of measurements throughout manufacturing operations.
Documentation and Record-Keeping
Rigorous documentation is a key aspect of effective calibration procedures. Maintenance teams maintain detailed records of calibration activities, including dates, results, and any adjustments made during the process. This documentation serves as a historical record, aiding in trend analysis and providing evidence of compliance during audits.
Training Personnel on Calibration Processes
Personnel involved in the calibration process must be adequately trained to perform procedures accurately. Training includes understanding the importance of calibration, following established protocols, and utilising calibration equipment correctly. Well-trained personnel contribute to the reliability of the calibration process and the accuracy of measurements.
Cleaning and Housekeeping Practices
The Impact of Cleanliness on Equipment Performance
Preventing Contamination and Corrosion
Cleanliness is more than aesthetics; it directly influences equipment performance. Regular cleaning helps prevent contamination and corrosion, especially in manufacturing environments where dust, debris, or chemical residues can accumulate. Contaminants can interfere with moving parts, compromise electrical components, and lead to accelerated wear. A clean environment ensures that equipment functions optimally and maintains its longevity.
Safety Considerations in Cleaning
Safety is paramount in manufacturing, and cleanliness contributes to a safer working environment. Cluttered or dirty spaces can increase the risk of accidents, slips, and falls. Additionally, clean equipment is easier to inspect, reducing the likelihood of overlooked safety hazards. Implementing proper cleaning practices aligns with occupational health and safety standards, fostering a workplace culture that prioritises the well-being of personnel.
Creating a Culture of Cleanliness
Beyond the immediate impact on equipment, promoting cleanliness contributes to building a culture of pride and responsibility among personnel. When employees recognise the importance of maintaining a clean workspace, they are more likely to adhere to housekeeping practices consistently. A culture of cleanliness extends beyond individual workstations to shared spaces, reinforcing a collective commitment to a safe and efficient manufacturing environment.
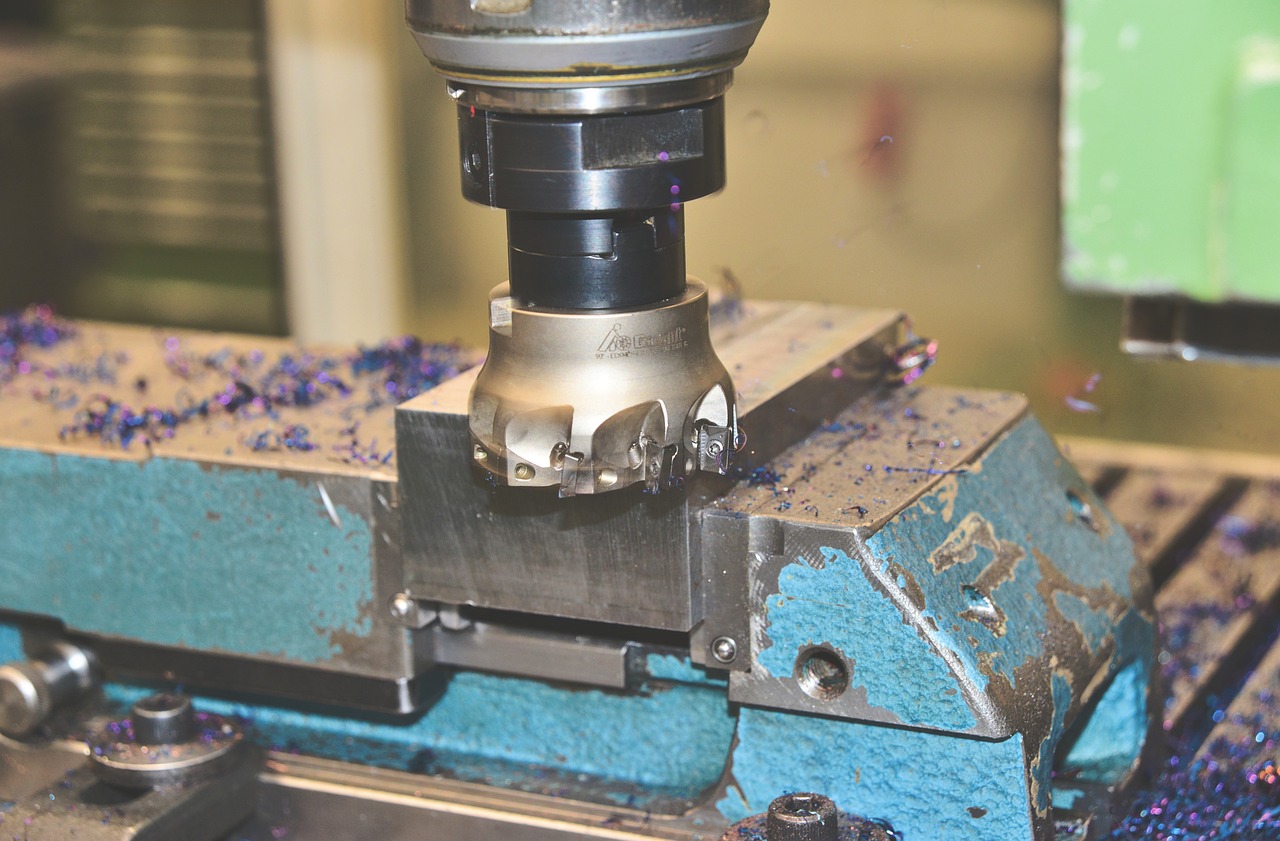
5.2 Developing Cleaning and Housekeeping Protocols
Regular Cleaning Schedules
Establishing regular cleaning schedules ensures that cleaning activities are consistent and thorough. These schedules can include daily, weekly, and monthly tasks, depending on the specific requirements of the manufacturing environment. High-traffic areas, machinery surfaces, and workspaces should be prioritised to prevent the accumulation of contaminants.
Proper Storage of Tools and Materials
Proper storage practices contribute to a clutter-free environment and facilitate efficient cleaning. Tools and materials should have designated storage areas, minimising the risk of misplaced items and creating clear pathways for personnel. Implementing organised storage also ensures that cleaning tools are readily available when needed, encouraging regular maintenance activities.
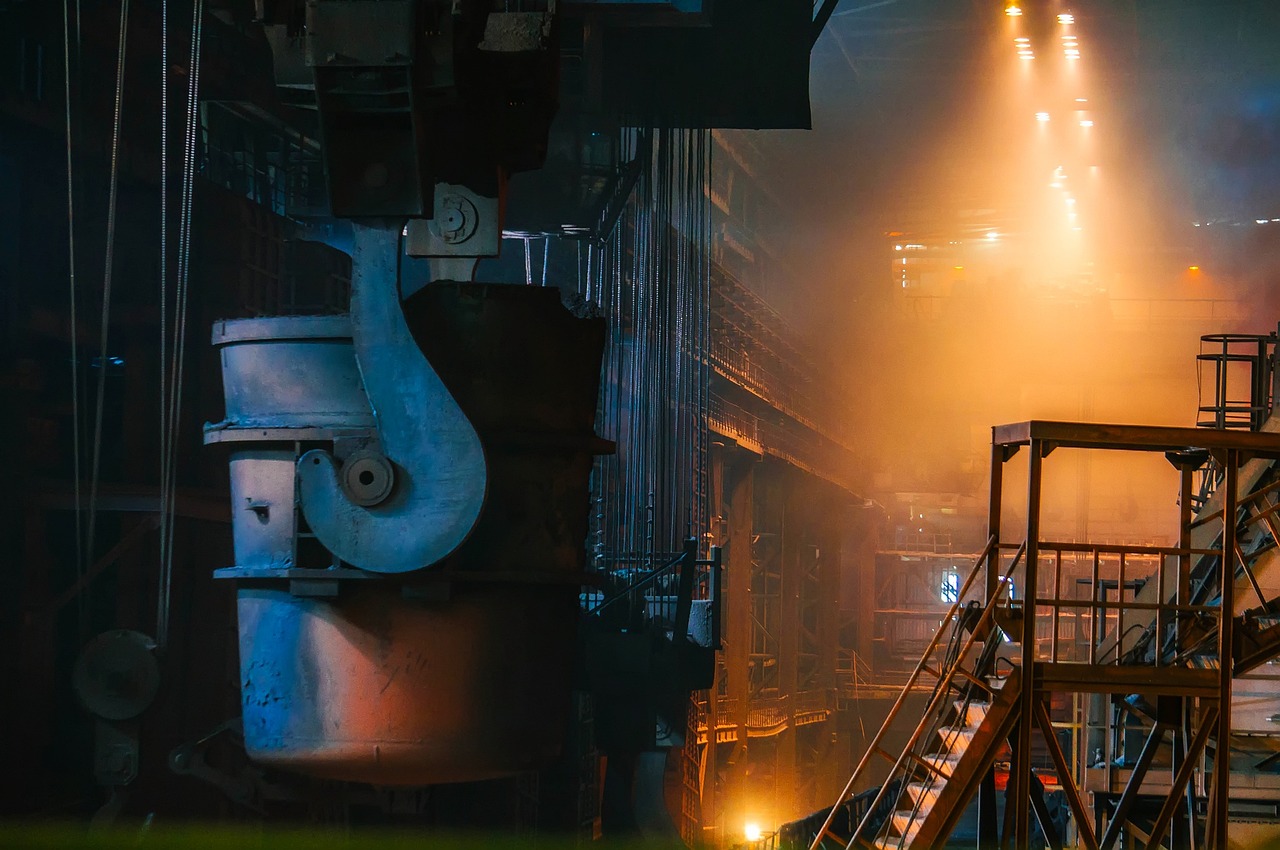
Involving Personnel in Housekeeping Practices
Personnel engagement is key to the success of housekeeping practices. Involving employees in the development of cleaning protocols and seeking their input fosters a sense of ownership. Training programs can educate personnel on the importance of cleanliness, proper cleaning techniques, and the impact on equipment performance. Recognition and rewards for adherence to housekeeping standards further motivate personnel to contribute actively to a clean and organised workspace.
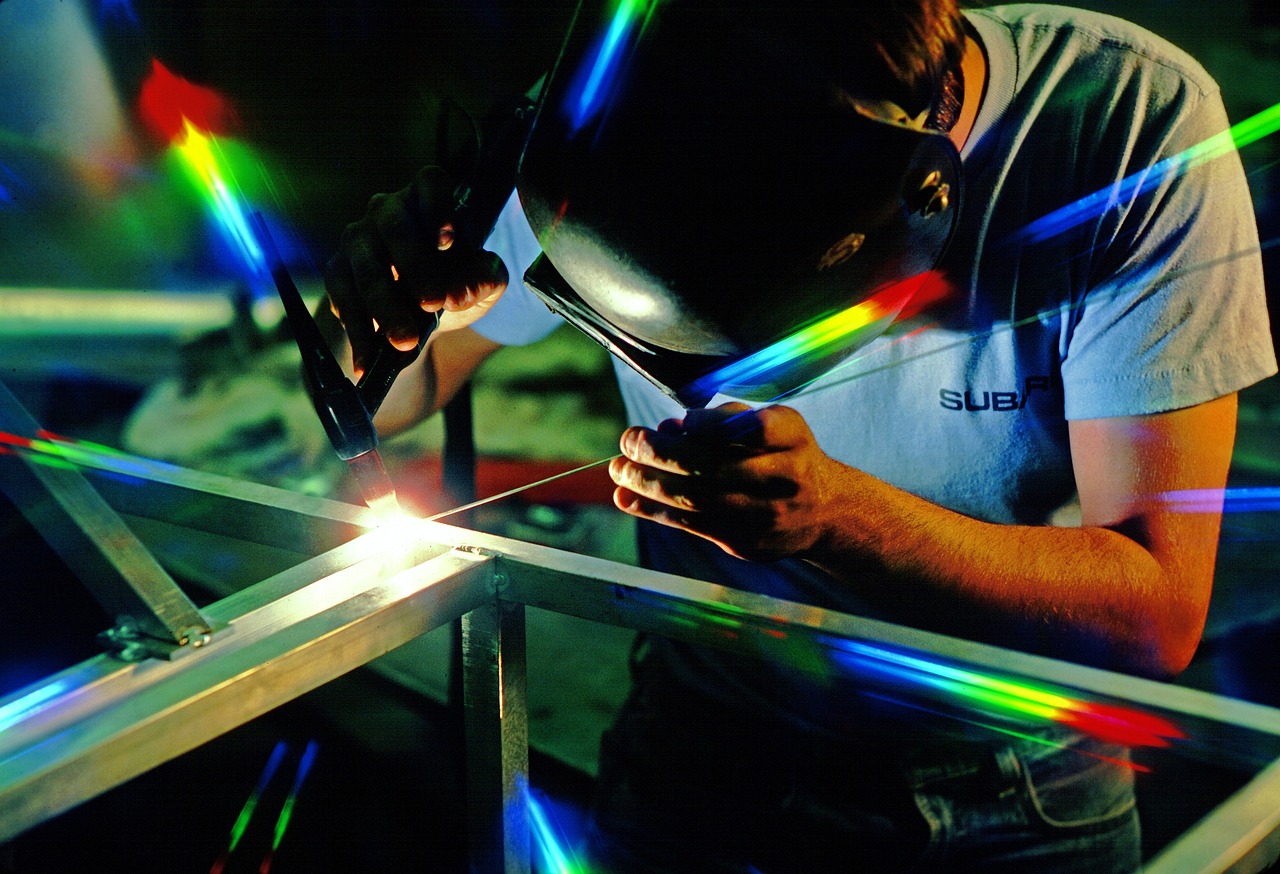
Recap of Key Preventive Maintenance Types
Throughout our exploration of preventive maintenance in manufacturing, we've delved into various crucial practices that collectively contribute to equipment reliability and operational efficiency. Let's recap the key preventive maintenance types discussed.
Routine Inspections |
Regular checkups to identify wear and tear, ensuring the early detection of potential issues. |
Lubrication Schedules |
Proper lubrication prevents friction, wear, and heat buildup, optimising the efficiency and lifespan of equipment. |
Component Replacement |
Component Replacement Identifying and replacing components prone to wear, with a focus on planned replacements to minimise downtime and costs. |
Component Replacement |
Identifying and replacing components prone to wear, with a focus on planned replacements to minimise downtime and costs. |
Calibration Procedures |
Ensuring the accuracy of measurements in manufacturing processes, complying with standards, and utilising predictive analytics for efficient scheduling. |
Cleaning and Housekeeping Practices |
Maintaining a clean and organised workspace to prevent contamination, corrosion, and safety hazards, fostering a proactive maintenance culture. |
Integrated Approach to Preventive Maintenance
Effective preventive maintenance goes beyond individual practices; it requires an integrated approach. The synergy of routine inspections, lubrication schedules, component replacement, calibration procedures, and cleaning practices creates a comprehensive maintenance strategy. Each type addresses specific aspects of equipment health, contributing to a holistic framework that enhances overall reliability and longevity.
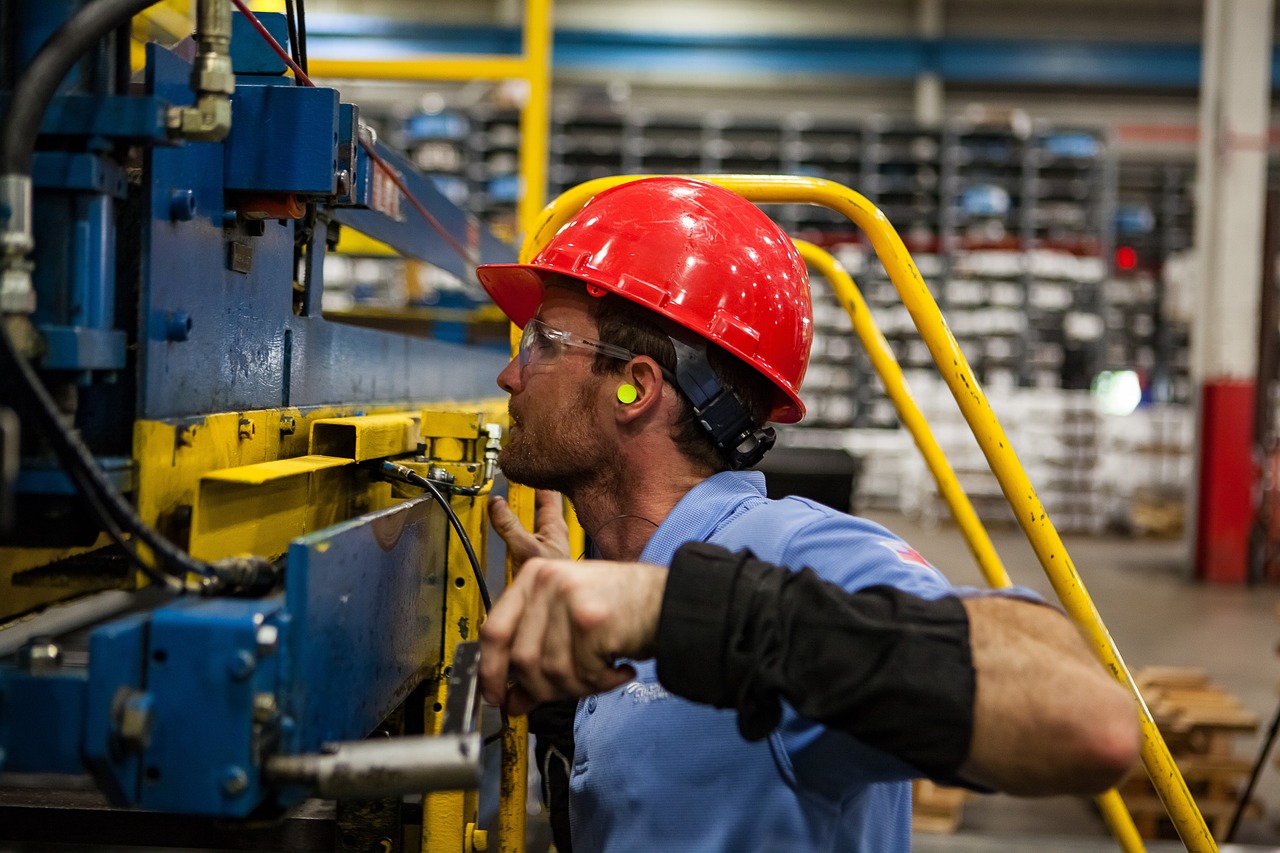
The Long-Term Benefits of Effective Preventive Maintenance
The benefits of effective preventive maintenance extend far beyond immediate operational concerns. Embracing these practices offers long-term advantages.
Reduced Downtime |
Planned maintenance minimises unplanned downtime, ensuring that equipment remains operational during critical production periods. |
Cost Savings |
Proactively addressing issues through preventive maintenance is often more cost-effective than reactive measures. It reduces emergency repair costs, extends equipment life, and optimises energy efficiency. |
Enhanced Product Quality |
Consistent equipment performance leads to improved product quality. Preventive maintenance contributes to the production of high-quality goods that meet or exceed customer expectations. |
Compliance and Safety |
Meeting regulatory standards through calibration procedures and maintaining a clean workspace enhances compliance and ensures a safe working environment for personnel. |
Encouraging a Proactive Maintenance Culture in Manufacturing
Fostering a proactive maintenance culture is fundamental to the success of preventive maintenance efforts. Key strategies include.
Training and Education |
Provide ongoing training to personnel on the importance of preventive maintenance, specific procedures, and the impact on overall operations. |
Employee Involvement |
Engaging employees in the development of maintenance protocols and recognising their contributions creates a sense of ownership and accountability. |
Continuous Improvement |
Encouraging a culture of constant improvement ensures that preventive maintenance strategies evolve with changing technology, industry standards, and equipment requirements. |
As manufacturing landscapes evolve, preventative maintenance becomes increasingly critical. Implementing these practices not only addresses immediate operational challenges but also positions manufacturing facilities for long-term success, sustainability, and resilience in an ever-changing market.
Comments
No comments yet!Add a Comment
You must be logged in to post a comment.