Step into manufacturing excellence, where we unravel the intricacies of Overall Equipment Effectiveness (OEE). As a key performance indicator, OEE is significant in assessing and refining manufacturing efficiency. This article is tailored specifically for the manufacturing audience, addressing the distinctive challenges in manual production processes. Our focal point revolves around introducing an optimal OEE hardware solution crafted to elevate manual production to new heights of efficiency and excellence. Join us in dissecting the relevance of OEE and unveiling hardware solutions uniquely designed for the manufacturing floor, promising transformative advancements in manual production processes.
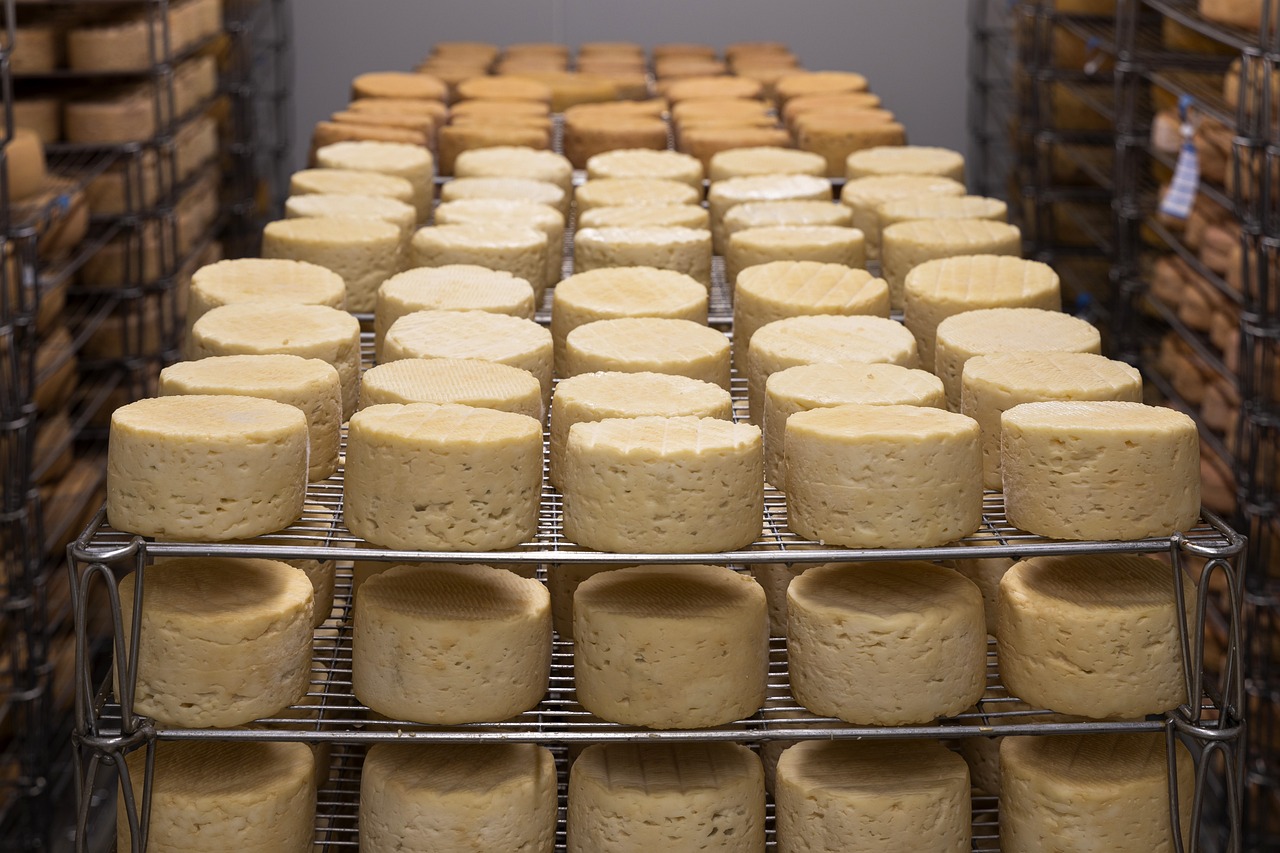
Understanding Manual Production Challenges
In the realm of manual production, a myriad of unique challenges demands a keen understanding of how to drive operational enhancements. From intricate tasks requiring human skill to the potential for variability in output quality, manual processes present a set of complexities distinct from automated counterparts. Navigating through these challenges becomes imperative for manufacturers aiming to achieve heightened efficiency. Whether it's mitigating the impact of human error, streamlining intricate workflows, or optimising resource allocation, addressing these challenges lays the foundation for an enhanced manual production landscape. This section sheds light on the nuanced difficulties inherent in manual production processes, emphasising the pivotal role of tailored solutions in overcoming these obstacles. As we delve into the intricacies of each challenge, the overarching objective remains clear — to pave the way for improved efficiency and excellence in manual production.
The Role of OEE in Manual Production
In the intricate landscape of manual production, Overall Equipment Effectiveness (OEE) emerges as a transformative force, reshaping the efficiency paradigm. At its core, OEE is a game-changer, offering a comprehensive lens through which manufacturers can gauge and elevate their operational performance.
OEE encapsulates three key metrics—Availability, Performance, and Quality—each playing a crucial role in the manual production environment. Availability measures the actual runtime against planned production time, highlighting downtimes that impede productivity. Performance scrutinises the pace at which production runs compared to its optimal speed, identifying inefficiencies in manual workflows. Lastly, Quality assesses the number of defect-free units, ensuring that manual tasks maintain the highest standards.
These metrics empower manufacturers in a manual production setting, where the human touch is intrinsic. By pinpointing areas of improvement, OEE acts as a guiding compass, steering operations towards enhanced productivity and reduced waste. The granular insights provided by OEE enable manufacturers to fine-tune manual processes, minimising downtimes, optimising workflows, and ultimately fostering a culture of continuous improvement. As we unravel the significance of OEE in manual production, it becomes evident that harnessing these metrics is instrumental in achieving newfound efficiency and excellence.
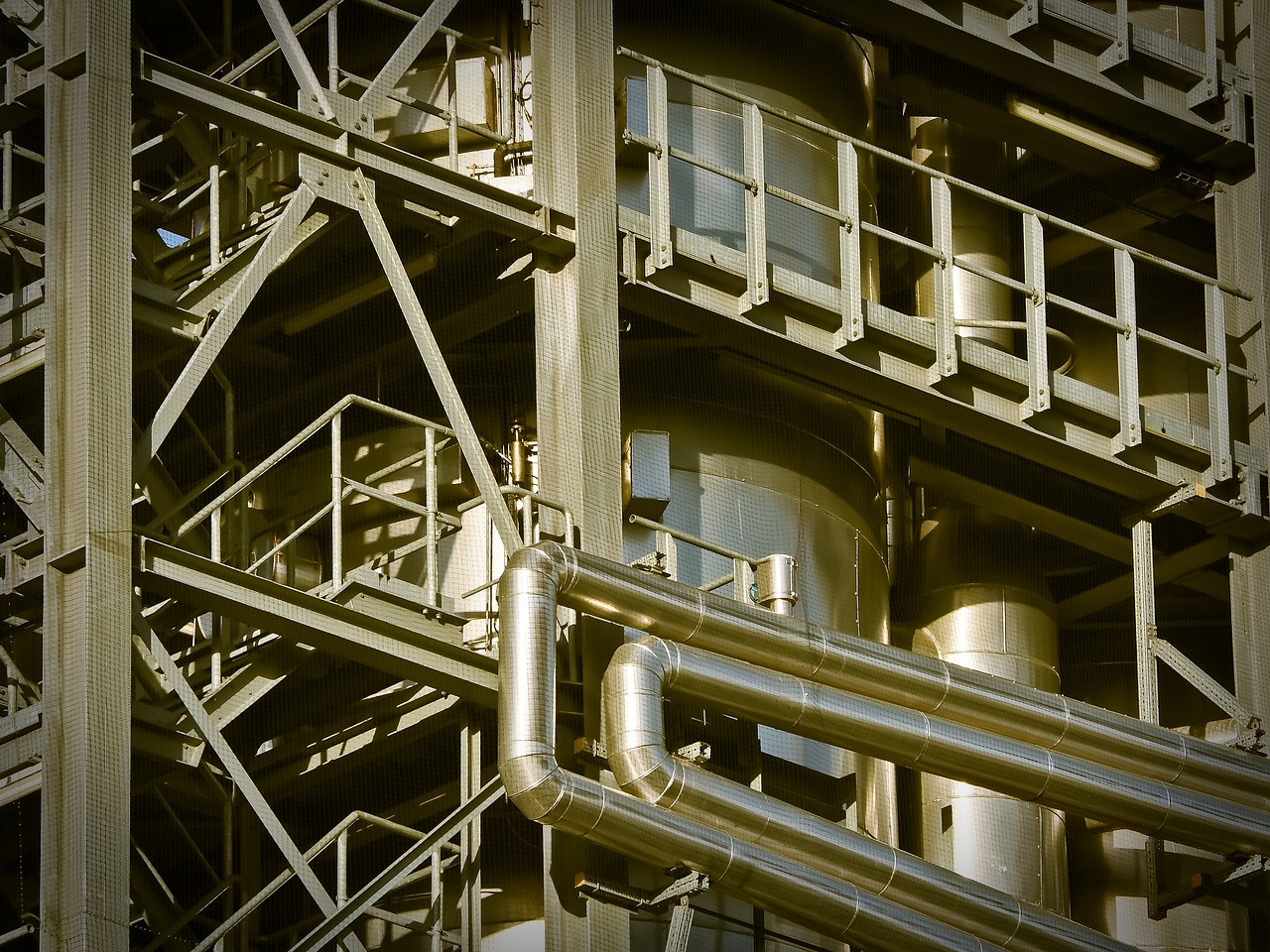
Criteria for the Perfect OEE Hardware
Selecting the right OEE hardware is pivotal in pursuing excellence in manual production. Several key criteria distinguish the perfect OEE hardware for manual workflows, each tailored to integrate seamlessly into the intricacies of manual production environments.
Ease of Integration
Efficiency begins with seamless integration. The perfect OEE hardware for manual production should integrate effortlessly with existing systems and processes. This ensures a smooth transition, minimising disruptions and allowing manufacturers to unlock the benefits of OEE without overhauling their established workflows.
User-Friendly Interfaces
Navigating the complexities of manual production demands user-friendly interfaces. The ideal OEE hardware simplifies data input and retrieval, empowering operators with intuitive interfaces. This user-centric design fosters engagement and ensures that valuable insights from the OEE system are easily accessible, contributing to informed decision-making on the manufacturing floor.
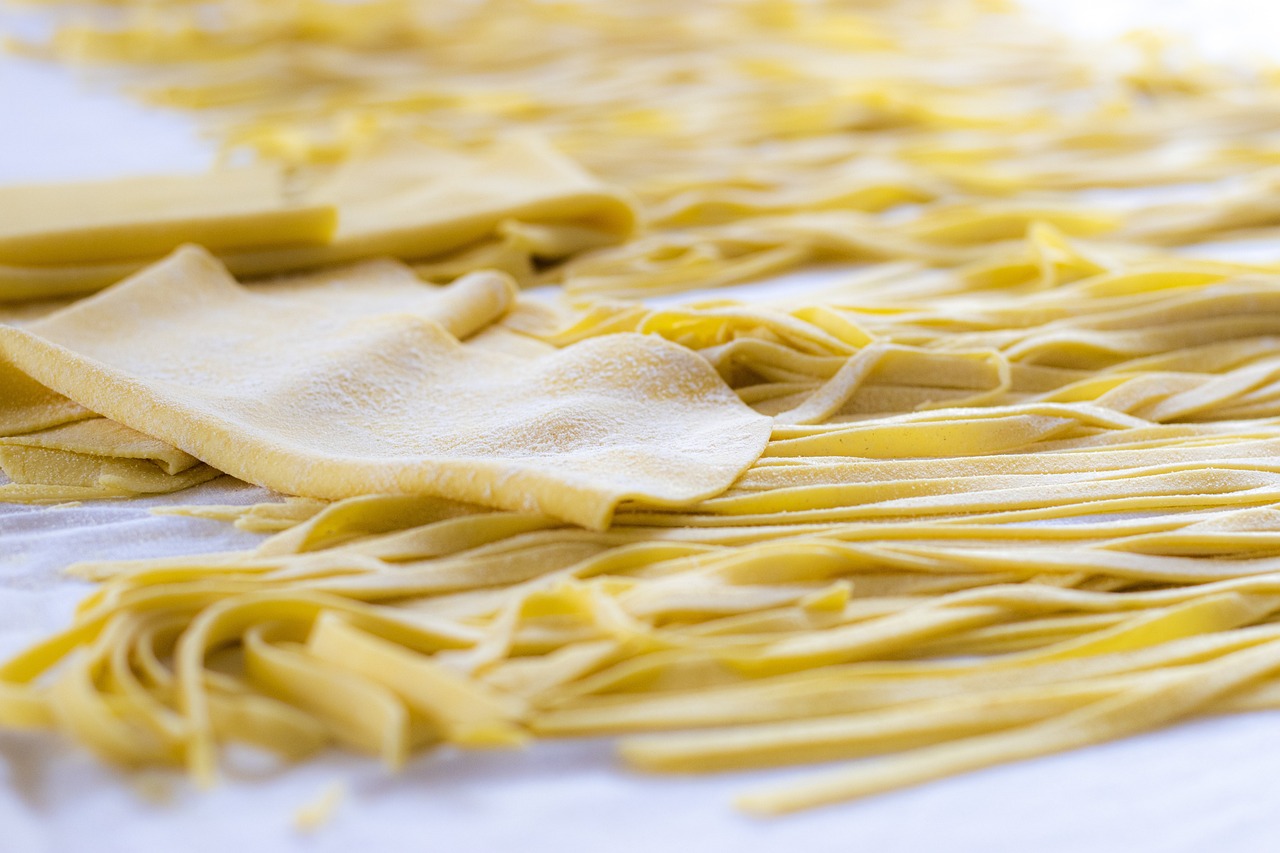
Adaptability to Manual Workflows
Manual production environments often involve dynamic and variable tasks. The perfect OEE hardware exhibits adaptability to these nuances. The hardware should be flexible, accommodating varying production rates or handling intricate manual processes. This adaptability ensures that OEE metrics accurately reflect the unique characteristics of manual workflows, offering insights tailored to the specific challenges and opportunities present in manual production.
As we dissect the criteria for the perfect OEE hardware, the emphasis remains on selecting a solution that aligns seamlessly with the manual production landscape. From integration to user interfaces and adaptability, these criteria collectively contribute to the effectiveness of the OEE hardware in driving efficiency and excellence in manual production processes.
Case Studies or Examples
Real-world implementations of OEE hardware in manual production settings are compelling testaments to its transformative power. Let's explore instances where OEE hardware has left an indelible mark on efficiency and productivity.
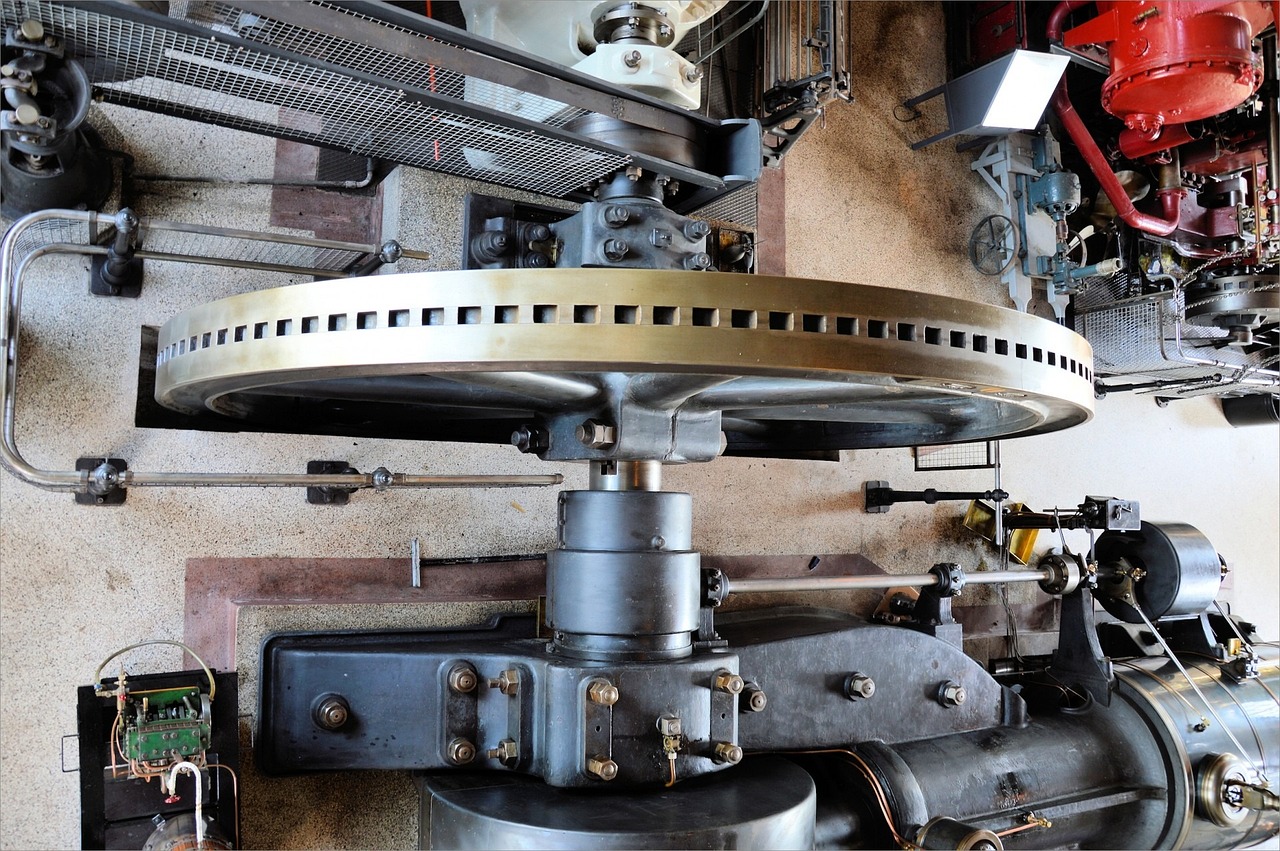
Streamlining Manual Workflows in Automotive Manufacturing
Integrating OEE hardware tailored for manual tasks in an automotive assembly plant led to significant improvements. The production team identified bottlenecks in manual assembly processes by closely monitoring the efficiency metrics, such as downtime and production rates. Adjustments were made, resulting in a notable reduction in downtime and a substantial increase in overall productivity.
Precision in Electronics Manufacturing
A case study in electronics manufacturing demonstrated how OEE hardware optimised manual tasks with intricate components. The hardware provided real-time insights into the performance of manual operators, ensuring precision in assembly and reducing the occurrence of defects. This precision elevated product quality and streamlined the overall production process.
Enhancing Craftsmanship in Furniture Production
In bespoke furniture manufacturing, where craftsmanship is paramount, OEE hardware tailored for manual workflows played a crucial role. By tracking and analysing the time taken for intricate woodworking tasks, the production team identified areas for skill development and process refinement. The result was a harmonious blend of craftsmanship and efficiency, showcasing how OEE hardware can enhance product quality and production speed.
These case studies exemplify how OEE hardware brings tangible improvements when thoughtfully implemented in manual production settings. The positive impact on efficiency and productivity is evident, underscoring the instrumental role of well-designed OEE hardware in elevating manual production processes to new levels of excellence.
Features to Look For
Selecting the perfect OEE hardware for manual production involves a nuanced understanding of essential features tailored to meet the unique demands of this environment. Delve into the key features that distinguish optimal OEE hardware in manual production settings, focusing on sensor technology, data accuracy, and reporting capabilities.
Advanced Sensor Technology
The ideal OEE hardware for manual production should harness advanced sensor technology. These sensors are pivotal in capturing real-time data on manual tasks, from assembly line operations to intricate craftsmanship. Whether monitoring manual dexterity or tracking the handling of components, advanced sensor technology ensures precise and granular data collection. This capability is foundational for deriving accurate OEE metrics that reflect the nuances of manual workflows.
Uncompromising Data Accuracy
Precision is paramount in manual production, and OEE hardware should uphold uncompromising data accuracy. Look for features that mitigate inaccuracies caused by variations in manual processes. Whether tracking the duration of manual tasks or identifying defects, the perfect OEE hardware guarantees reliable and precise data. This accuracy forms the cornerstone for informed decision-making and targeted improvements in manual production efficiency.
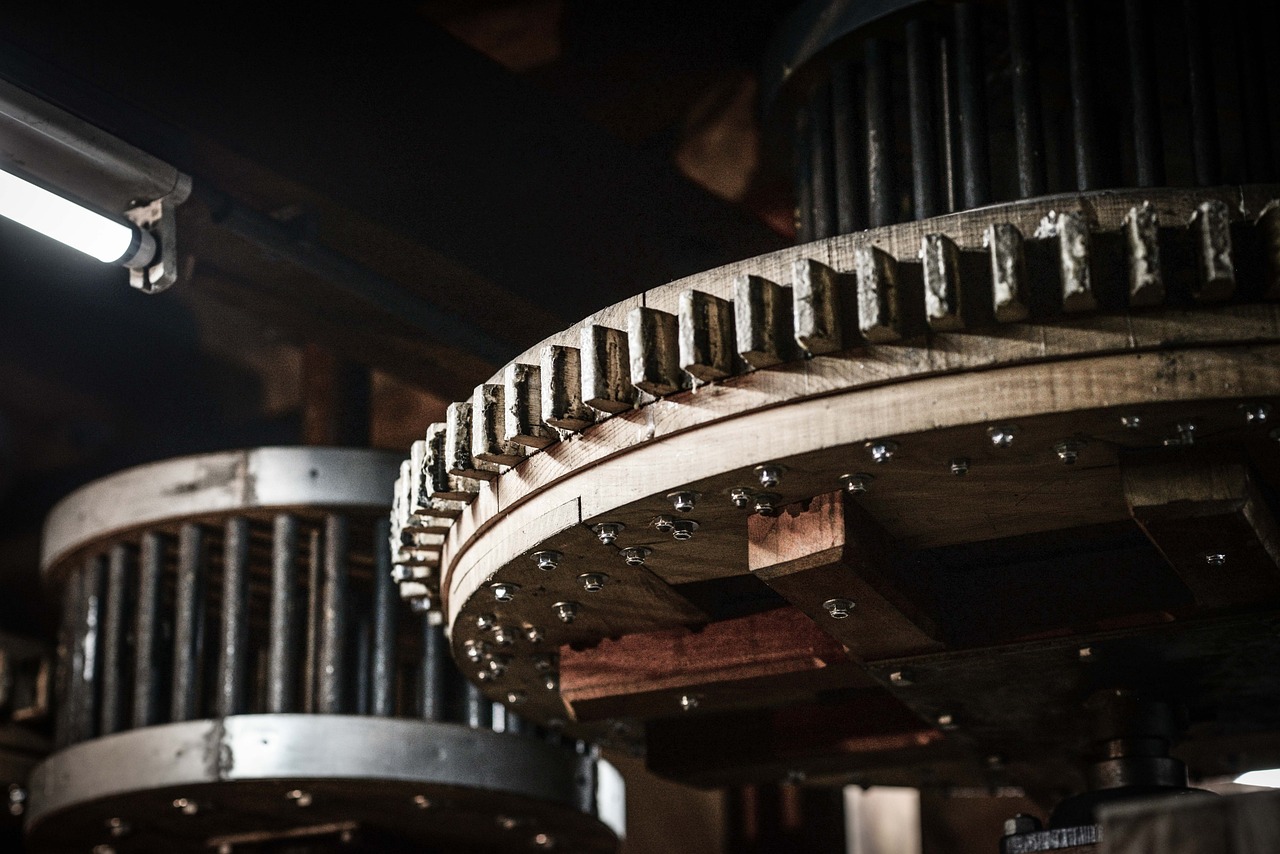
Robust Reporting Capabilities
To derive actionable insights, the OEE hardware should boast robust reporting capabilities. Effective visualisation of OEE metrics, downtime analyses, and productivity trends empowers decision-makers to identify patterns and areas for enhancement. Look for reporting customisable features, providing flexibility in tailoring analyses to the specific needs of manual production environments. This ensures that the data generated by the OEE hardware translates into meaningful and actionable intelligence.
As manufacturers navigate the landscape of OEE hardware for manual production, a keen focus on these features ensures the selection of a solution that aligns seamlessly with the intricacies of manual workflows. From sensor technology to data accuracy and reporting capabilities, these features collectively contribute to the effectiveness of OEE hardware in driving efficiency and excellence in manual production processes.
Implementation Tips
Implementing OEE hardware in a manual production setup requires a strategic approach to harness its full potential. Here are practical tips and guidelines to ensure a smooth integration, along with insights on overcoming potential challenges:
Comprehensive Training Programs
Initiate comprehensive training programs for operators and production staff. Ensure that they are well-versed in the functionalities of the OEE hardware, understand the significance of collected metrics, and are proficient in utilising the system to its fullest capacity. A well-trained team is key to maximising the benefits of OEE in a manual production environment.
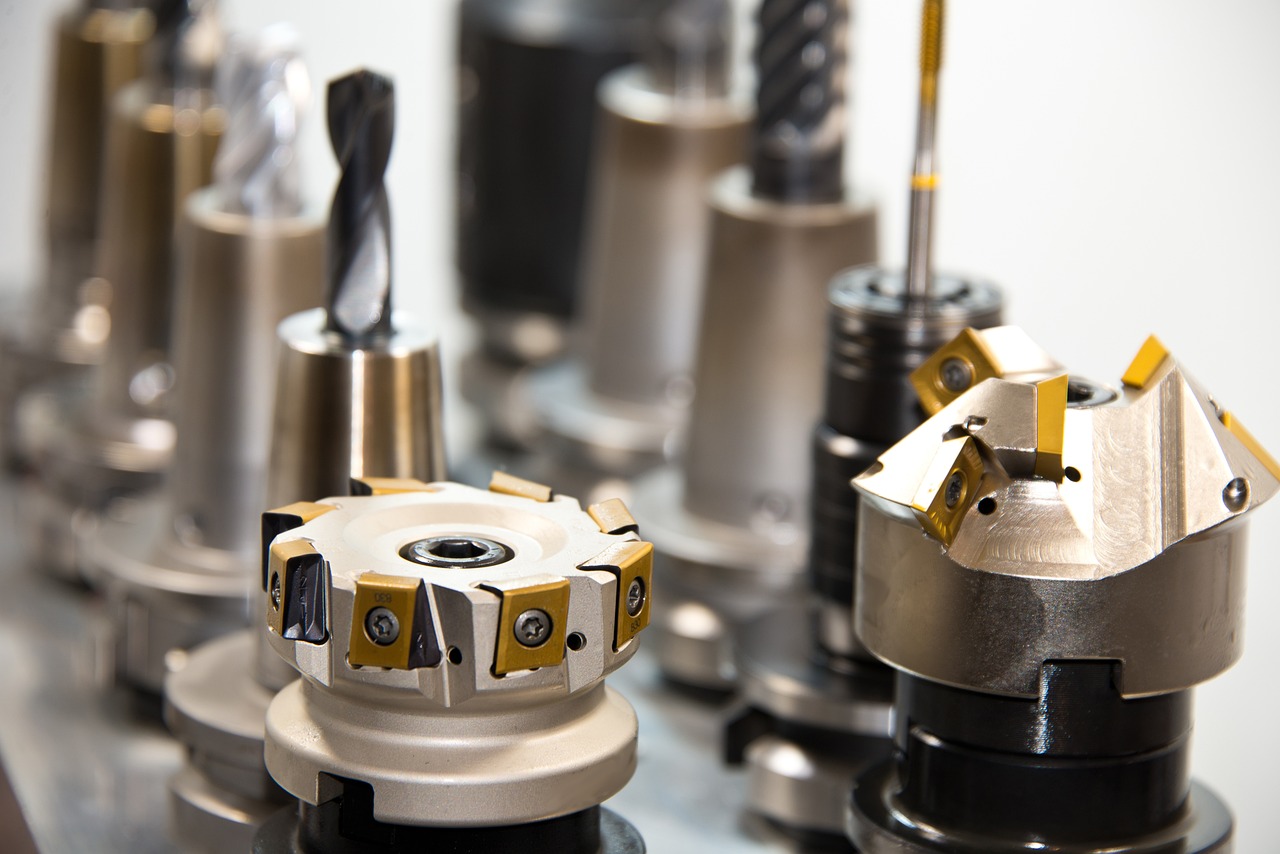
Establish Clear Communication Protocols
Transparent communication is essential during the implementation phase. Clearly articulate the objectives and expected outcomes of integrating OEE hardware. Establish open lines of communication between production operators, management, and IT personnel to address queries and concerns promptly, fostering a collaborative environment.
Conduct a Pilot Implementation
Consider a pilot implementation in a controlled environment before scaling up. This allows for a focused evaluation of how the OEE hardware interacts with manual workflows and provides an opportunity to fine-tune the system based on real-time feedback. A pilot phase minimises disruptions and ensures a more streamlined integration when fully deployed.
Address Data Security Concerns
Given the sensitive nature of production data, prioritise data security. Implement robust cybersecurity measures to safeguard the integrity and confidentiality of production metrics. Collaborate with IT experts to establish secure data transmission and storage protocols, ensuring that the implementation of OEE hardware aligns with industry standards and regulations.
Overcoming Resistance to Change
Resistance to change is a common challenge in any implementation process. Communicate the benefits of OEE hardware, emphasising how it contributes to operational efficiency and individual roles. Foster a culture of openness to innovation and provide ongoing support to address concerns, gradually winning over stakeholders and ensuring a smoother transition.
Navigating these implementation tips facilitates a successful integration of OEE hardware and helps anticipate and address potential challenges effectively. By following these guidelines, manufacturers can position themselves for a seamless and impactful utilisation of OEE in their manual production setups.
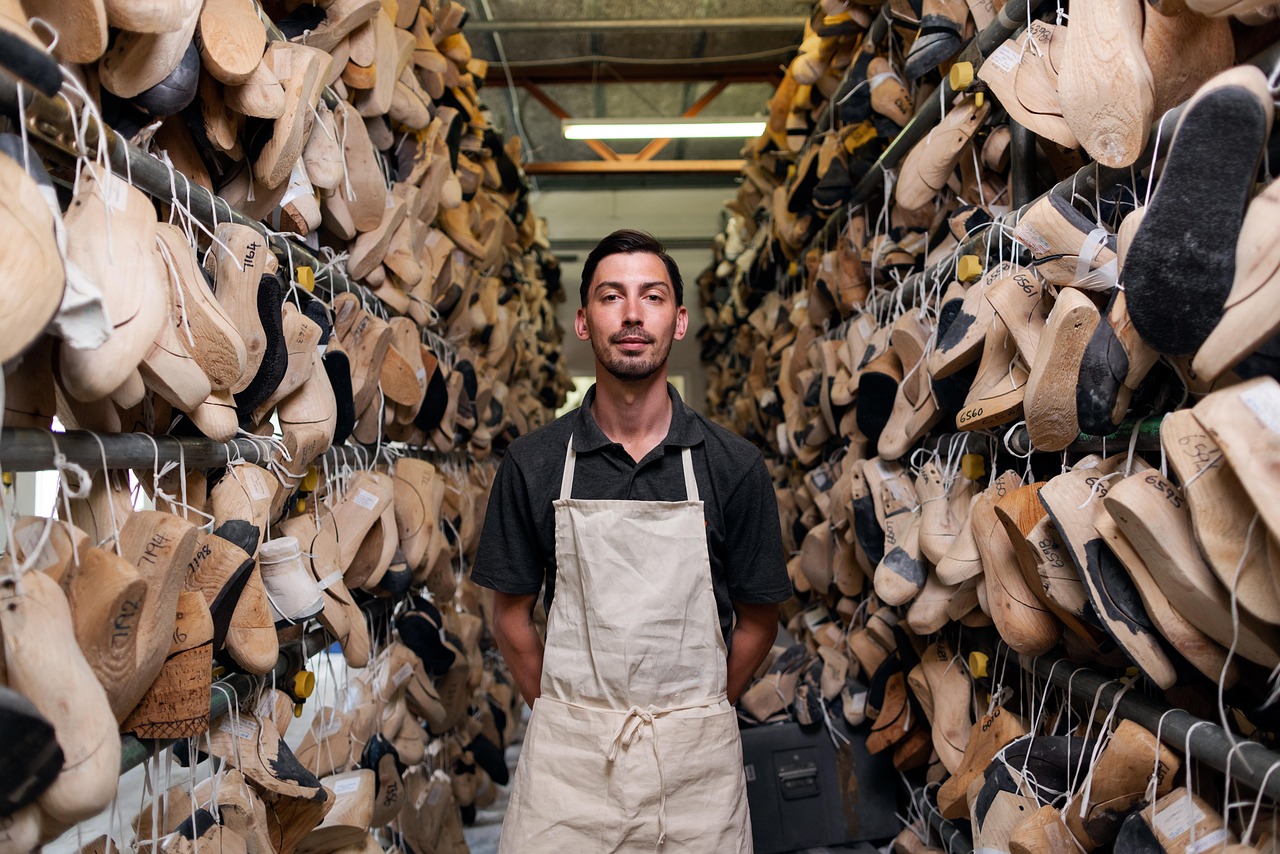
Future Trends and Innovations
As the manufacturing landscape evolves, staying ahead of emerging trends and innovations in OEE hardware for manual production is crucial for sustained success. Let's explore the future and discuss the importance of staying updated.
Integration with Industry 4.0 Technologies
The future of OEE hardware lies in seamless integration with Industry 4.0 technologies. Look for innovations that leverage the Internet of Things (IoT), artificial intelligence, and advanced analytics to enhance the capabilities of OEE hardware. These integrations enable real-time monitoring, predictive maintenance, and adaptive production strategies, further optimising manual workflows.
Cloud-Based Solutions for Accessibility
Cloud-based OEE solutions are gaining prominence, providing accessibility from anywhere with an internet connection. This trend ensures stakeholders, including managers and decision-makers, can access critical production metrics remotely. Cloud-based OEE hardware fosters collaboration and enables quick decision-making, particularly in dynamic manual production environments.
Enhanced Human-Machine Collaboration
Future OEE hardware innovations will prioritise enhancing human-machine collaboration. This entails creating intuitive interfaces that empower manual operators by providing actionable insights in real-time. User-friendly systems that seamlessly integrate human decision-making with machine-driven analytics contribute to improved overall production efficiency.
Continuous Software Updates and Support
Staying updated involves more than hardware innovations; it extends to continuous software updates and support. Choose OEE hardware solutions from providers committed to ongoing improvements, ensuring your system remains compatible with evolving industry standards and requirements. Regular updates also address potential vulnerabilities and introduce new features, contributing to the long-term success of your implementation.
Remaining abreast of these future trends and innovations is not just a strategic choice; it is necessary for manufacturers aspiring to achieve and sustain excellence in manual production. By adopting forward-thinking OEE hardware solutions, companies can position themselves at the forefront of industry advancements, driving long-term success and resilience in an ever-changing manufacturing landscape.
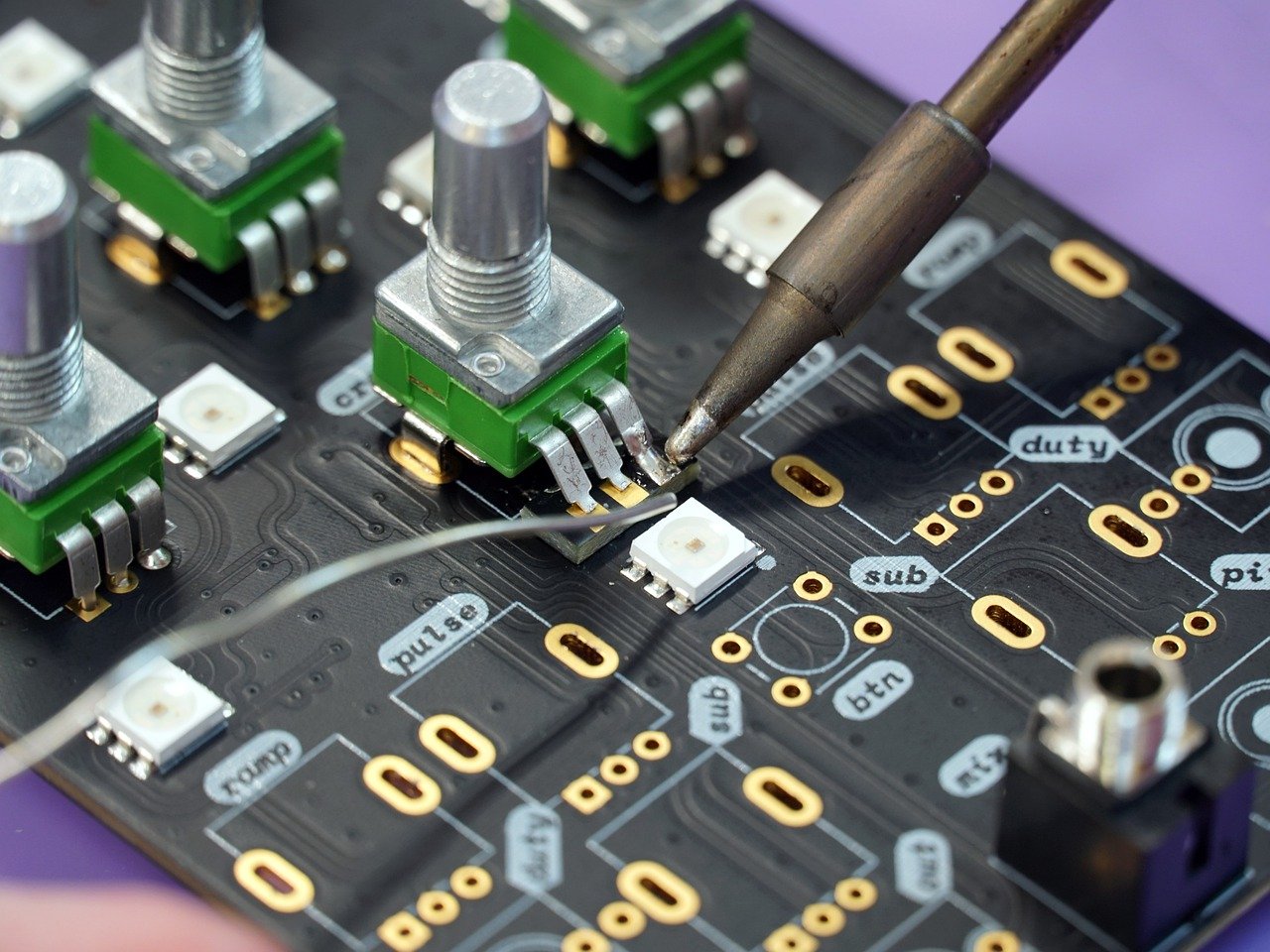
Conclusion
In conclusion, our journey through the intricacies of Overall Equipment Effectiveness (OEE) and its application in manual production has unveiled key insights and considerations. From understanding the challenges unique to manual workflows to exploring the crucial role of OEE metrics, we have navigated a landscape where precision and efficiency converge.
The quest for the perfect OEE hardware has been central to our exploration, emphasising its pivotal role in elevating manual production to unprecedented levels of excellence. From ease of integration to advanced sensor technology, the criteria for selecting the right OEE hardware are intricately woven into the fabric of manual production environments.
Through real-world case studies, we witnessed the tangible impact of OEE hardware on efficiency and productivity in diverse manufacturing settings. These success stories underscore the transformative power of well-implemented OEE solutions, showcasing their ability to streamline workflows, mitigate challenges, and enhance overall operational performance.
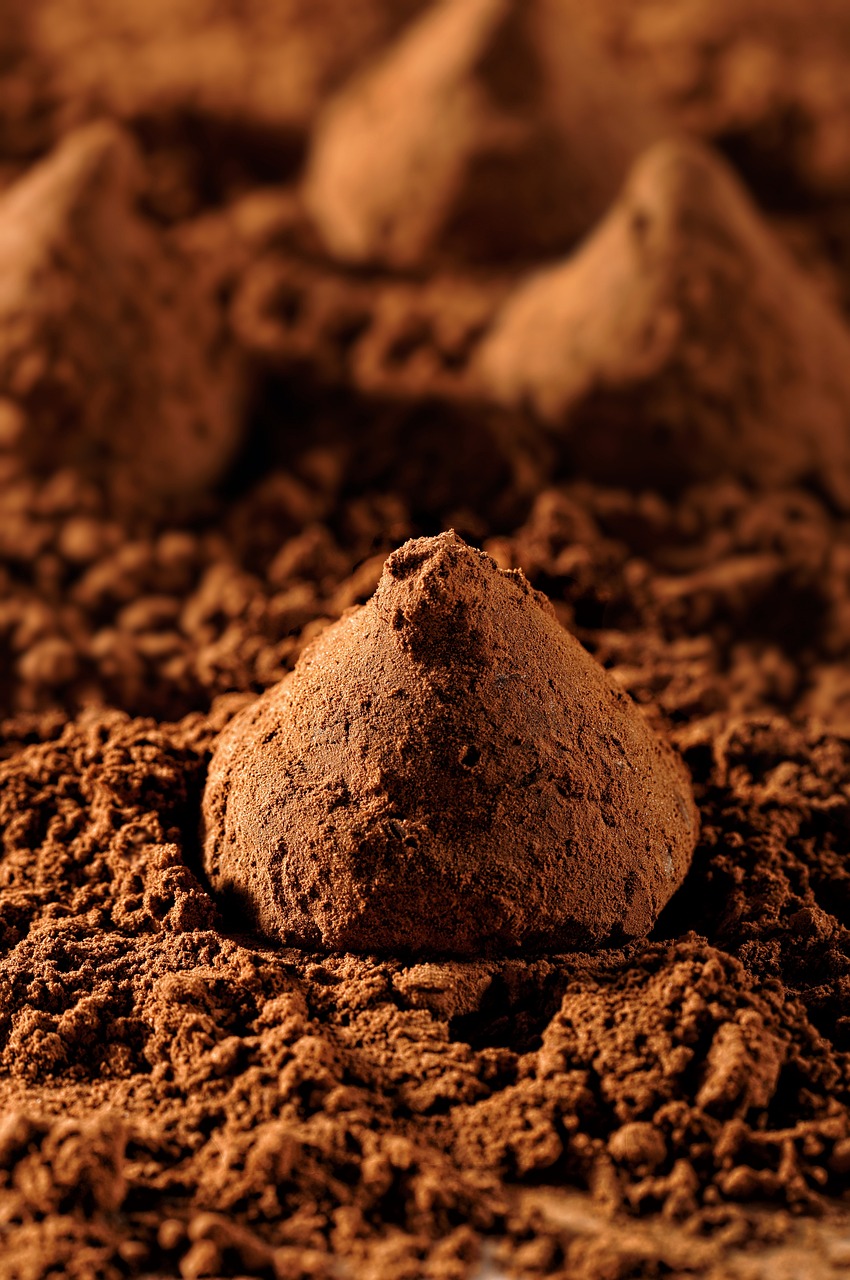
As we peer into the future, the convergence of OEE with Industry 4.0 technologies, cloud-based solutions, and a focus on human-machine collaboration beckons a new era in manual production efficiency. Staying updated with these emerging trends is not just a strategic choice but a necessity for manufacturers aspiring to lead in an ever-evolving industry landscape.
Implementing OEE hardware in manual production is a technological upgrade and a catalyst for excellence. The perfect OEE hardware is a guiding force, aligning manual workflows with precision and efficiency. It empowers manufacturers to make informed decisions, adapt to dynamic challenges, and drive a culture of continuous improvement.
As you implement OEE hardware in your manual production processes, remember that it's not just a tool; it's a cornerstone for excellence, laying the foundation for a future where every manual task contributes seamlessly to the overarching success of your production endeavours.
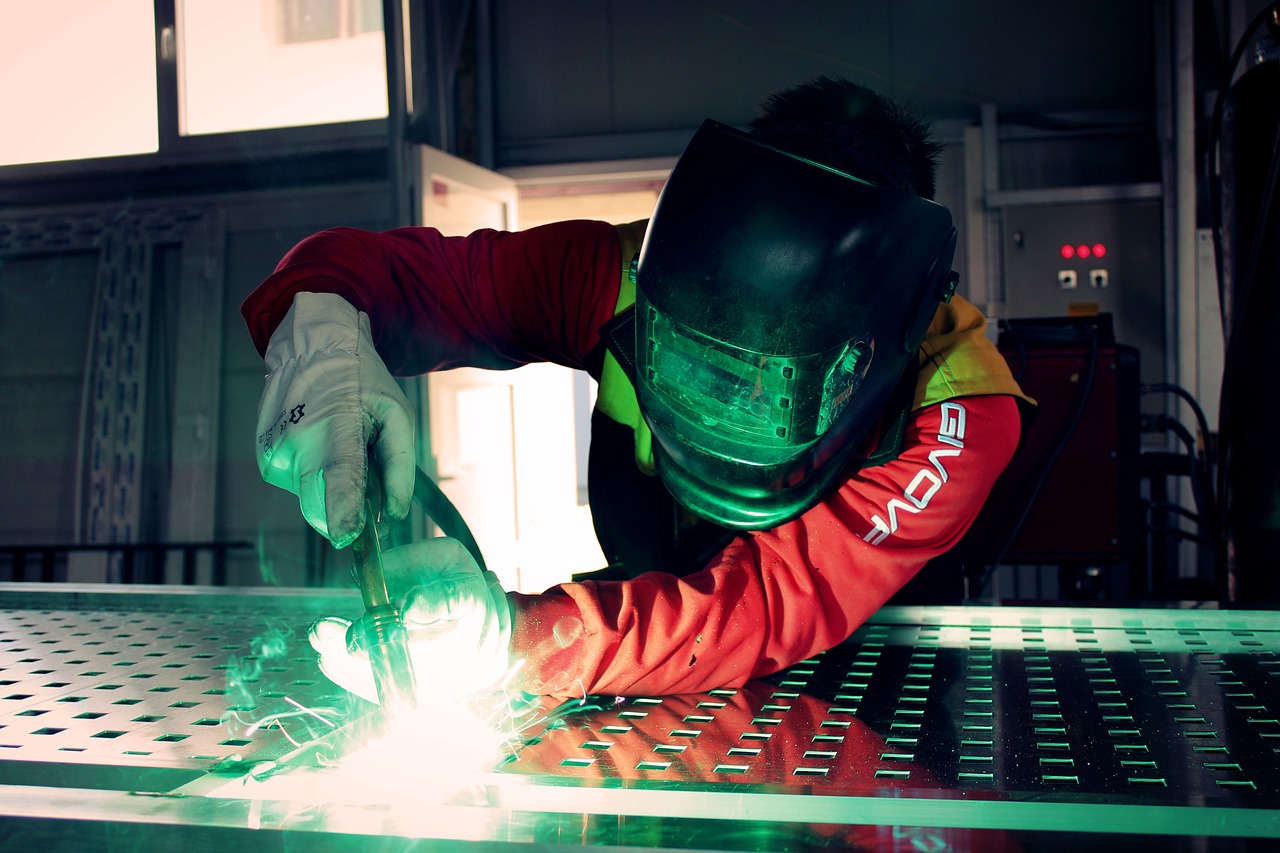
Comments
No comments yet!Add a Comment
You must be logged in to post a comment.